随着半导体行业的发展,晶体管尺寸缩小至纳米级,集成度大幅提高。然而,量子隧穿效应和原子级加工难题制约了摩尔定律的发展。智能化时代对芯片轻量化和高集成化的需求推动了2.5D/3D集成技术的发展,其中玻璃通孔(TGV)技术因其优异的电学性能和机械稳定性,成为下一代三维集成的关键技术。
TGV技术以硼硅玻璃、石英玻璃等为基材,通过通孔成型、种子层溅射、电镀填充等工艺实现3D互连。由于玻璃基板硬度高、脆性大,制备高深宽比、侧壁无缺陷的通孔是极大挑战。目前,玻璃通孔的制造方法包括喷砂工艺、超声波钻孔、湿法腐蚀、等离子体刻蚀、聚焦放电、激光钻孔等,各有优缺点。
喷砂法是一种比较传统且简单的玻璃通孔加工方式,属于磨料流加工方法的一种,是通过高速喷射束将磨料喷射到玻璃表面从而产生刻蚀的过程。通常需要在玻璃表面沉积金属或聚合物掩膜来保护非加工区域。在 TGV工艺中,常见的磨料为A12O3,其颗粒直径通常为5〜100μm。
喷砂法适合制作大尺寸玻璃通孔,对小尺寸及小间距、高深宽比TGV形成具有一定的限制,且制作的通孔一致性较差,表面粗糙度大,目前已逐渐淡出三维集成封装的应用范畴。
超声波钻孔是一种机械加工法,其原理是利用超声波振头,将能量通过磨料传递至玻璃表面,以冲击、研磨的方式去除表面材料,从而实现通孔制备。制备玻璃通孔的尺寸、质量等与钻头的尺寸、振动频率、磨料尺寸等密切相关。适用于加工低深宽比、大孔径的通孔,一般能制作的最小孔径在76μm左右,材料去除速度低,一般不超过3mm³/s。
在半导体工艺中,湿法腐蚀是制备玻璃微结构最常用的方法,湿 法腐蚀易于操作、设备简单且成本低廉。在湿法腐蚀工艺中,掩膜一般选择抗氢氟酸(H F)腐蚀的金(Au)以及等离子体增强化学气相沉积 (PECVD)生 长的低温 SiC、多晶硅以及光刻胶等。
湿法腐蚀中容易发生侧壁钻蚀现象,制备的玻璃通孔一般锥度比较大,因 此在小尺寸及小间距的玻璃通孔制备中比较少见。
国内外的学者们在等离子体刻蚀玻璃方面进行了大量的研究,玻璃的主要成分为 SiO2,刻蚀气体主要是氟基气体(如碳氟气体、SF₆等 )与Ar、He等不同附加气体的组合,其刻蚀是物理刻蚀和化学刻蚀相结合的结果。
图2 等离子刻蚀法制作的玻璃通孔
相对于湿法腐蚀,等离子体刻蚀工艺可以实现较高深宽比的通孔,但是其工艺过程复杂、耗时长、制作成本高。
聚焦放电法和电化学放电法
聚焦放电法和电化学放电法放电法是一种通过局部放热作用产生玻璃通孔的过程。涉及玻璃通孔加工的放电法主要有聚焦放电法 (EDM)和电化学放电法 (ECDM)两种。
聚焦放电法通过放电控制和聚焦作用对玻璃的局部区域熔融,然后利用焦耳热诱发玻璃内部产生高压并引起介质击穿和内部高压,使玻璃熔液蒸发 并喷射出来。
图3 聚焦放电法制备的TGV SEM图及原理图
电化学放电法是结合电解加工和电火花加工的制作工艺,用碱性电解质溶液的电化学放电和化学腐蚀产生的热量对玻璃局部区域熔融。

图4 电化学放电法中使用的针尖阵列及制备的玻璃通孔
聚焦放电法通常只需要0.3〜0.6s就可以在厚度180〜300 的玻璃上制作一个通孔。电化学放电法法加工的 TGV孔径一般多在 200μm以上。
聚焦放电和电化学放电法都属于串行加工方式,即每个放电点对应一个微孔,通过使用多电极尖端阵列可以同时加工多个通孔,提高加工速度,而这种多针尖阵列多为定制化工具,因此适用性比较单一,且制造的通孔的形状都不是很垂直。
激光烧蚀法也叫激光钻孔,利用激光在玻璃内部产生强烈的原子振动而使得玻璃迅速升温,从而使得玻璃原子脱落基底并被烧蚀挥发的过程。玻璃 在可见光范围内的吸收率一般比较低,为了提高效率,激光钻孔一般使用红外或紫外波段的激光。
目前有使用CO₂激光器、266nm/355nm紫外激光器和波长193nm的 ArF激光器等技术来制备玻璃通孔。
日本三菱电机通过特殊的玻璃表面处理技术,利用高峰值功率脉冲 CO₂激光器在厚度 100 的玻璃上制备了直径 25 的通孔 ,如图5(b)所示,孔的边缘存在微裂纹。
图5 激光器烧蚀法制备的玻璃通孔形貌图
光敏玻璃法是一种光刻-腐蚀法,容易获得较高的深宽比和通孔密度,在工艺便捷性和集成度上具有一定的优势。通过调节光敏玻璃的成分及优化曝光参数,可制备最小孔径20深宽比30:1的高密度通孔。
光敏玻璃属于一种特殊玻璃,难以制作大尺寸基板,如知名玻璃厂商肖特生产的光敏玻璃 FOTURAN®II 最大尺寸为 175mm X175mm,因此利用光敏玻璃法制备 TGV 的成本较高。
据报道,玻璃材料在超快激光的照射下形成纳米孔洞,即激光影响区域(LAZ),该区域具有很高的化学反应活性,使得 LAZ在氢氟酸或者碱性溶液的湿法腐蚀中的刻蚀速度明显高于未受激光修饰的区域。利用超短脉冲激光的飞秒激光刻蚀法或者选择性激光腐蚀 (SLE)可明显降低常规通孔加 工过程中的热应力以及裂纹等缺陷,但是激光器的产出能力有限,加工时间比较长,且加工的玻璃材料一般以熔融石英为主。
德国LPKF公司提出了一种高精度的激光诱导深度刻蚀 (LIDE)技术,使用超快激光加工玻璃基板,单个脉冲即可完成整个玻璃厚度的改性。LIDE技术不局限于某些特 定成分的玻璃,几乎适用于所有SiO₂基玻璃。
①根据设计图形,使用超快激光在玻璃上产生修饰区域;
②将激光处理过的玻璃放到腐蚀液中进行刻蚀形成通孔。
LIDE被认为是一种极具潜力的 TGV加工技术,并已经得到大量的研究及应用,如康宁、肖特、Samtec和国内的厦门云天半导体等。LIDE可在50〜1000μm 厚的玻璃基板上加工最小直径 5μm 的通孔,加工精度达微米量 级,深宽比可达 100:1,通孔锥度范围根据玻璃种类的不同可达 0.1°〜30°。LIDE加工效率高,每秒可加工 5000个通孔。
与传统钻出的微孔相比,玻璃通孔激光诱导刻蚀制造的玻璃通孔没有微裂纹、 碎裂和热应力。LIDE技术与其他半导体工艺具有较高的兼容性,在 3D集成和晶圆级封装领域具有很大的应用潜力。
玻璃通孔成型技术是目前 TGV技术的重难点,下表是几种主要的成孔方法的优缺点比较。
TGV技术在半导体领域应用广泛,包括扇出型封装、三维立体封装和系统级封装等,尤其在射频、光电子、MEMS等领域具有巨大潜力。玻璃基板因其优异的电学性能和机械稳定性,成为理想的封装材料,支持高频应用、光学检测和光路集成。
其在半导体领域的应用方式主要包括:作为永久支撑的玻璃衬底,通过薄膜技术在玻璃上制备各种图形和结构;作为传感器的封装盖板;制作各种晶圆级光学元件,如折射型或衍射型光学元件;作为临时衬底的玻璃载体,为硅器件晶圆提供机械支撑;作为 3D TGV中介层或者基板,利用通孔实现垂直电气互连。
TGV技术是实现 5G 时代三维集成的关键,在先进封装领域具有很大的应用前景,广泛应用于 MEMS传感器、光电器件、微流体器件等领域。
目前 TGV 的开发应用在欧美日成熟度最高,国内也有部分企业进行此技术工艺的开发,并取得了一定的成果。
知名玻璃制造商康宁公司多年来一直致力于玻璃解决方案的研究,可提供超大尺寸的玻璃面板,为先进半导体封装提供带过孔的精密玻璃。
AGC是全球领先的玻璃供应商 ,可以根据客户要求的图案在薄玻璃基板上制作通孔。
LPKF公司研发的 LIDE技术是一项在微系统中广泛应用的新技术,每秒可加工 5000个通孔,最小孔径可达5μm。
美国Samtec拥有核心玻璃通孔技术,其密封式 TGV 由高品质硼硅酸盐玻璃、熔融石英和蓝宝石制成。
WOP是全球顶级的飞秒激光微加工供应商之一 ,在飞秒激光微加工方面可达亚微米级别的精度。
其他的如鈦昇科技、日本江东电气 、TECNISCO等也致力于 TGV 领域研究,为玻璃基板提供解决方案。
除此之外,肖特、美国乔治亚理工学院、德国 Fraunhofer IZM研究院、新加坡微电子研究所等国际领先的玻璃材料供应商和半导体研究机构都对 TGV技术进行了深人的研究。
国内方面,厦门云天半导体可以在厚度50〜500μm的玻璃上生产直径 7μm 的通孔 ,深宽比可达70:1,锥度接近 90°,可满足射频、光通信、毫米波等领域应用。
沃格光电拥有玻璃基巨量微米级通孔的加工能力,最小孔径可至10μm,线宽小至8μm。
成都迈科的核心TGV技术最小孔径可达7μm,深宽比为50:1。大族半导体、帝尔激光等公司都在 TGV加工领域有显著的成果及进展。
玻璃基板虽然具有优异的物理特性,如高平整度、低热膨胀系数等,但其硬度大、脆 性高的特点也增加了加工难度。如何在保证性能的同时,降低 加工难度,提高良品率 ,是玻璃基板生产中的一大挑战。未来需要持续研究更先进的玻璃基板加工技术,提高加工精度、降低损伤风险、提高加工效率以及降低加工成本。
来源:刘丹, 乌李瑛, 田苗, 等. 玻璃通孔成型工艺及应用的研究进展[J]. 微纳电子技术
艾邦建有玻璃基板与TGV技术交流群,可以加强产业链的合作,促成各企业的需求对接,同时您也可以与行业精英共同探讨玻璃基板及TGV技术的前沿动态,共享资源,交流经验,欢迎您的加入。
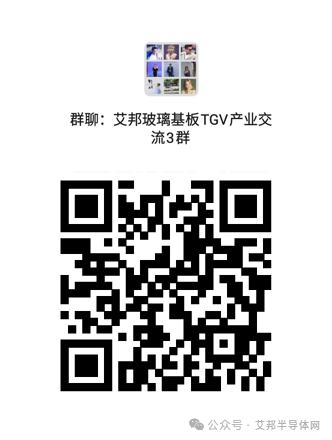
Nico 肖:136 8495 3640(同微信)
邮箱:ab012@aibang.com
方式二:长按二维码扫码在线登记报名
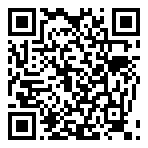
或者复制网址到浏览器后,微信注册报名:
https://www.aibang360.com/m/100230?ref=172672
点击阅读原文即可报名玻璃基板论坛!
我们诚邀您加入“玻璃基板与TGV技术交流群”,与行业精英共同探讨玻璃基板及TGV技术的前沿动态,共享资源,交流经验。在这里,您可以第一时间获取技术革新信息,深入解析行业趋势,与行业领袖面对面交流,共同推动技术革新,探索无限商机。
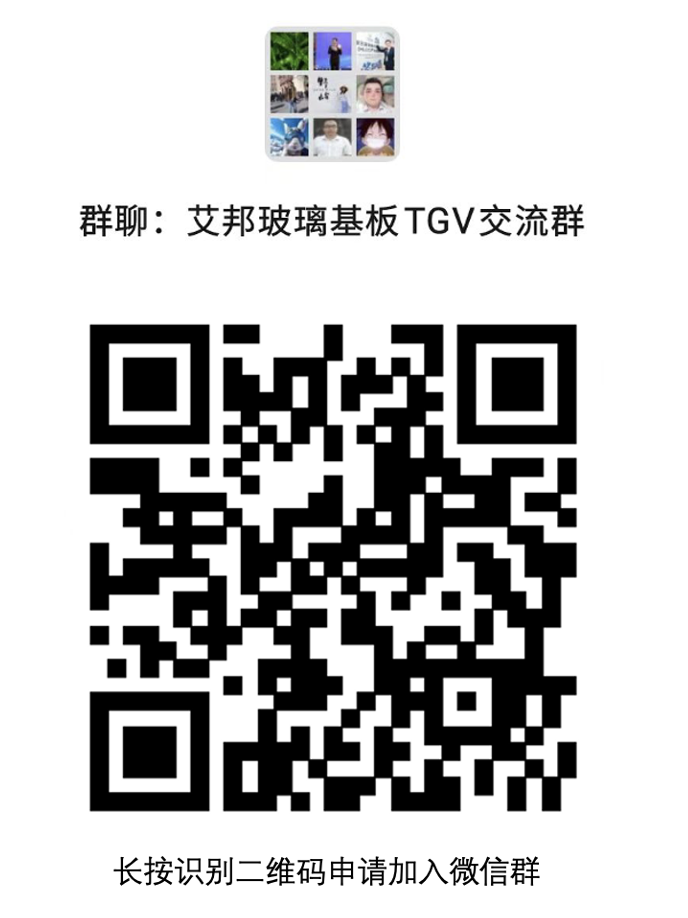