

前言

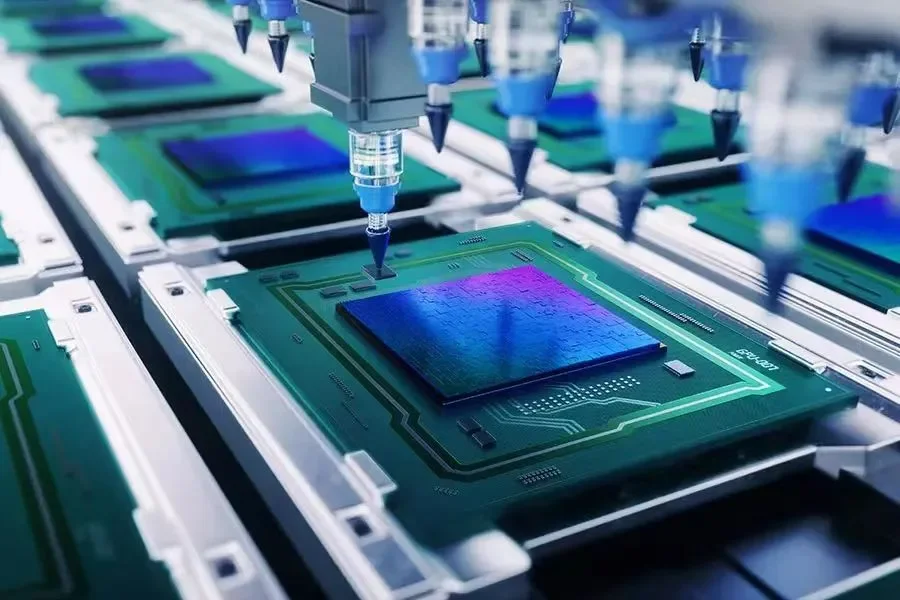
作为新型功率半导体器件的主流器件,IGBT应用非常广泛,如家用电器、电动汽车、铁路、充电基础设施、充电桩,光伏、风能,工业制造、电机驱动,以及储能等领域。
IGBT模块是新一代的功率半导体电子元件模块,诞生于20世纪80年代,并在90年代进行新一轮的改革升级,通过新技术的发展,现在的IGBT模块已经成为集通态压降低、开关速度快、高电压低损耗、大电流热稳定性好等等众多特点于一身,而这些技术特点正式IGBT模块取代旧式双极管成为电路制造中的重要电子器件的主要原因。
近些年,电动汽车的蓬勃发展带动了功率模块封装技术的更新迭代。目前电动汽车主逆变器功率半导体技术,代表着中等功率模块技术的先进水平,高可靠性、高功率密度并且要求成本竞争力是其首先需要满足的要求。


功率器件模块封装结构演进趋势


IGBT作为重要的电力电子的核心器件,其可靠性是决定整个装置安全运行的最重要因素。由于IGBT采取了叠层封装技术,该技术不但提高了封装密度,同时也缩短了芯片之间导线的互连长度,从而提高了器件的运行速率。
按照封装形式和复杂程度,IGBT产品可以分为裸片DIE、IGBT单管、IGBT模块和IPM模块。
1、裸片DIE:由一片晶圆切割而成的多颗裸片DIE;
2、IGBT单管:由单颗DIE封装而成的IGBT分立器件,电流能力小,适用于家电等领域;
3、IGBT模块:由多颗DIE并联封装而成,功率更大、散热能力更强,适用于新能源汽车、高铁、光伏发电等大功率领域;
4、IPM模块:在IGBT模块外围增加其他功能的智能功率模块(IPM);
IGBT被称成为“功率半导体皇冠上的明珠”,广泛应用于光伏电力发电、新能源汽车、轨道交通、配网建设、直流输电、工业控制等行业,下游需求市场巨大。IGBT的核心应用产品类型为IGBT模块。IGBT模块的市占率能够达到50%以上,而IPM模块和IGBT单管分别只有28%左右和20%左右。从产品的投资价值来看,由于IGBT模块的价值量最大,有利于企业快速提升产品规模,其投资价值最大。


IGBT应用领域


实现IGBT国产化,不仅需要研发出一套集芯片设计、晶圆制造、封装测试、可靠性试验、系统应用等于一体的成熟工艺技术,更需要先进的工艺设备。
随着芯片减薄工艺的发展,对封装提出了更高的要求。封装环节关系到IGBT是否能形成更高的功率密度,能否适用于更高的温度、拥有更高的可用性、可靠性,更好地适应恶劣环境。
IGBT模块封装是将多个IGBT集成封装在一起,以提高IGBT模块的使用寿命和可靠性,体积更小、效率更高、可靠性更高是市场对IGBT模块的需求趋势。常见的模块封装技术有很多,各生产商的命名也不一样,如英飞凌的62mm封装、TP34、DP70等等。一个IGBT模块的封装需经历贴片、真空焊接、等离子清洗、X-RAY照线光检测、键合、灌胶及固化、成型、测试、打标等等的生产工序。
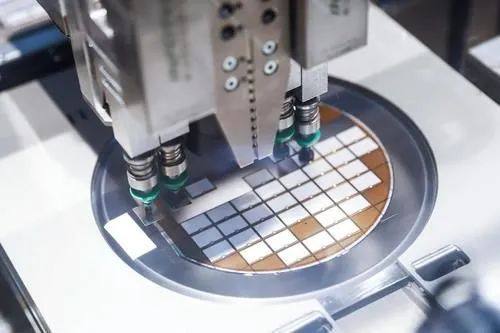
IGBT封装工艺流程


IGBT模块封装流程简介


2、自动贴片:将IGBT芯片与FRED芯片贴装于DBC印刷锡膏表面;
IGBT封装环节包括:丝网印、贴片、键合、功能测试等环节。这其中任何一个看似简单的环节,都需要高水准的封装技术和设备配合完成。
例如贴片环节,将IGBT芯片与FRED芯片贴装于DBC印刷锡膏表面。这个过程需要对IGBT芯片进行取放,要确保贴片良率和效率,就要求以电机为核心的贴片机具有高速、高频、高精力控等特点。
随着新能源汽车行业的高速发展,对高功率、高密度的IGBT模块的需求急速增加,很多汽车厂商都已走上了IGBT自研道路,以满足整车生产需求,不再被上游产业链“卡脖子”。
要生产具有高可靠性的IGBT模块,高精度芯片贴装设备必不可少。
3、真空回流焊接:将完成贴片的DBC半成品置于真空炉内,进行回流焊接;
高质量的焊接技术,才能生产出高可靠性的产品。一般回流焊炉在焊接过程中会残留气体,并在焊点内部形成气泡和空洞。超标的焊接气泡会对焊点可靠性产生负面的影响,包括:
(1) 焊点机械强度下降;
(2) 元器件和PCB电流通路减少;
(3)高频器件的阻抗增加明显;
(4)导热性降低导致元器件过度升温。
真空回流焊接工艺是在回流焊接过程中引入真空环境的一种回流焊接技术,相对于传统的回流焊,真空回流焊在产品进入回流区的后段,制造一个真空环境,大气压力可以降到 5mbar(500pa)以下,并保持一定的时间,从而实现真空与回流焊接的结合,此时焊点仍处于熔融状态,而焊点外部环境则接近真空,由于焊点内外压力差的作用,使得焊点内的气泡很容易从中溢出,焊点空洞率大幅降低。低的空洞率对存在大面积焊盘的功率器件尤其重要,由于高功率器件需要通过这些大面积焊盘来传导电流和热能,所以减少焊点中的空洞,可以从根本上提高器件的导电导热性能。
4、超声波清洗:通过清洗剂对焊接完成后的DBC半成品进行清洗,以保证IGBT芯片表面洁净度满足键合打线要求求。
5、X-RAY缺陷检测:通过X光检测筛选出空洞大小符合标准的半成品,防止不良品流入下一道工序;
6、自动键合:通过键合打线,IGBT芯片打线将各个IGBT芯片或DBC间连结起来,形成完整的电路结构。
半导体键合AOI主要应用于WB段后的检测,可为IGBT生产提供焊料、焊线、焊点、DBC表面、芯片表面、插针等全面的检测。
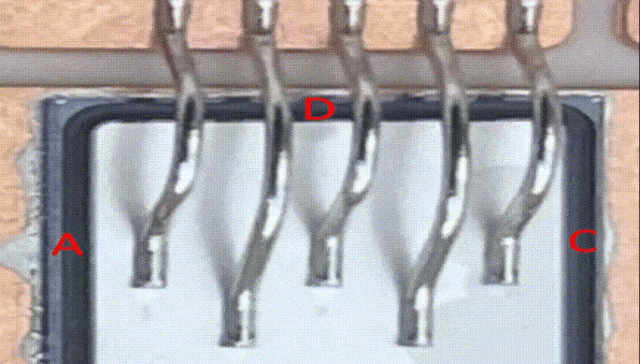
▲高精度还原线弧
7、激光打标:对IGBT模块壳体表面进行激光打标,标明产品型号、日期等信息;
8、壳体塑封:对壳体进行点胶并加装底板,起到粘合底板的作用;
9、功率端子键合
10、壳体灌胶与固化:对壳体内部进行加注A、B胶并抽真空,高温固化 ,达到绝缘保护作用;
11、封装、端子成形:对产品进行加装顶盖并对端子进行折弯成形;
12、功能测试:对成形后产品进行高低温冲击检验、老化检验后,测试IGBT静态参数、动态参数以符合出厂标准 IGBT 模块成品。
功率半导体模块封装是其加工过程中一个非常关键的环节,它关系到功率半导体器件是否能形成更高的功率密度,能否适用于更高的温度、拥有更高的可用性、可靠性,更好地适应恶劣环境。功率半导体器件的封装技术特点为:设计紧凑可靠、输出功率大。其中的关键是使硅片与散热器之间的热阻达到最小,同样使模块输人输出接线端子之间的接触阻抗最低。
IGBT模块的封装技术难度高,高可靠性设计和封装工艺控制是其技术难点。IGBT模块具有使用时间长的特点,汽车级模块的使用时间可达15年。因此在封装过程中,模块对产品的可靠性和质量稳定性要求非常高。高可靠性设计需要考虑材料匹配、高效散热、低寄生参数、高集成度。封装工艺控制包括低空洞率焊接/烧结、高可靠互连、ESD防护、老化筛选等,生产中一个看似简单的环节往往需要长时间摸索才能熟练掌握,如铝线键合,表面看只需把电路用铝线连接起来,但键合点的选择、键合的力度、时间及键合机的参数设置、键合过程中应用的夹具设计、员工操作方式等等都会影响到产品的质量和成品率。
集成电路产业链包括芯片设计、晶圆制造、芯片封装和测试等环节,各个细分环节目前都 已经发展成为独立的子行业。按照集成电路产品的生产制造过程进行划分,IC 设计行业 是集成电路行业的上游。IC 设计企业设计产品方案,通过代工方式由晶圆代工厂 Foundry、 封装厂商和测试厂商完成芯片的制造、封装和测试,然后将芯片产成品作为元器件销售给 电子设备制造厂商。
集成电路测试服务行业上游的测试机、探针台等设备主要由美国、日本的海外设备厂商垄 断。测试服务厂家主要分为两类:1)封测厂自有测试产线;2)专业的第三方测试公司。芯片设计厂商是芯片测试服务行业的主要客户,以 SoC/MCU/FPGA 等设计行业为主。早期 的 IC 设计公司会将订单直接下达至封测厂,再由封测厂外包至第三方的集成电路测试公 司,随后逐步演进为 IC 设计公司直接下订单至第三方测试公司。
晶圆测试(Chip Probing),简称 CP,是指通过探针台和测试机的配合使用,对晶圆上的 裸芯片(gross die)进行功能和电学性能参数的测试。测试过程主要为:探针台将晶圆 逐片传送至测试位置,芯片端点通过探针、专用连接线与测试机的功能模块进行连接,测试机对芯片施加输入信号并采集输出信号,以判断芯片功能和性能是否达到设计规范要求。对裸片的测试结果通过通信接口传送至探针台,探针台会根据相应的信息对芯片进行打点 标记,形成晶圆的 Mapping,即晶圆的电性能测试结果。CP 测试设备主要由支架、测试机、 探针台、探针卡等部件组成。CP 测试会统计出晶圆上的芯片合格率、不合格芯片的确切位 置和各类形式的良率等,可用于指导芯片设计和晶圆制造的工艺改进。
芯片成品测试(Final Test),简称 FT,FT 测试是在芯片封装后按照测试规范对电路成品 进行全面的电路性能检测,目的是挑选出合格的成品芯片,保障芯片在任何环境下都可以 维持设计规格书上所预期的功能及性能。通过分选机和测试机配合使用,测试过程主要为:分选机将被测芯片逐个传送至测试工位,被测芯片的引脚通过测试工位上的基座、专用连 接线与测试机的功能模块进行连接,测试机对芯片施加输入信号并采集输出信号,判断芯 片功能和性能是否达到设计规范要求。测试结果通过通信接口传送至分选机,分选机据此 对被测芯片进行标记、分选、收料或编带。FT 测试系统通常由支架、测试机、分选机、测 试板和测试座组成。FT 测试环节的数据可以用于指导封装环节的工艺改进。
CP 测试的主要目的在于挑出坏的裸片,减少后续的封装和 FT 测试成本;FT 测试的主要目 的确保芯片符合交付要求,避免将不合格的芯片交付给下游用户。相比于 FT 测试,CP 测 试精密度要求更高、技术要求更高、难度更大。芯片在完成封装后处于良好的保护状态, 体积也较晶圆状态的裸片增加几倍至数十倍,因此 FT 测试对洁净等级和作业精细程度的 要求较 CP 测试低一个级别,但测试作业的工作量和人员用工量更大。CP 测试和 FT 测试 在确保芯片良率、控制生产成本、指导 IC 设计和生产工艺改进等方面都起到了至关重要 的作用。
1.2AI 芯片加大 Chiplet 等先进封测需求,芯片测试 “量价齐升”
在 AI 浪潮下,算力是生成式 AI 核心。GPU 可以通过并行化矩阵运算,使得生成式 AI 中 庞大的语言模型能够同时处理海量数据,从而显著加快了训练时间。目前龙头公司英伟达 的新产品GB200已经采用Chiplet方案,将两个GPU和一个CPU相连形成一个“Blackwell” 芯片,与上一代 H100 相比,有望将训练性能提高 4 倍,推理性能提高 30 倍。
此外,AMD 的 MI300 同样采用 CPU+GPU 合封的 Chiplet 方式,单卡硬件性能出色。MI300A 成为全球首个为 AI 和 HPC 打造的 APU 加速卡。采用 Chiplet 设计,拥有 13 个小芯片,基 于 3D 堆叠,包括 24 个 Zen4 CPU 内核,同时融合了 6 颗 CDNA 3 GPU 和 8 个 HBM3,集成 了 5nm 和 6nm IP,总共包含 128GB HBM3 显存和 1460 亿晶体管。根据 AMD 发布会,MI300A 相比上一代产品 MI250X 在 AI 算力上是上一代的 8 倍,而在单位能耗的 AI 运算上是上一 代的 5 倍。MI300X 没有集成 CPU,而是集成 8 个 GPU 以及 8 个 HBM 内存模组,其集成的晶 体管数量达到了 1530 亿。
在 AI 算力芯片的设计中,Chiplet 相较于 SoC 对于性能提升更有优势、性价比更高,有 望成为 AI 芯片设计公司的主流设计方案。Chiplet 具体是指小型模块化芯片,通过 dieto-die 内部互联技术将多个模块芯片与底层基础芯片封装在一起形成一个整体的内部芯 片。与 SoC 不同,SoC 是在设计阶段将不同的模块设计到一颗 die(芯片裸片)中,晶圆 制造完成后封装;Chiplet 则将不同模块从设计时就按照不同计算或者功能单元进行分解, 制作成不同 die 后使用先进封装技术互联封装,不同模块制造工艺可以不同。
Chiplet 相比传统 SoC 芯片优势明显。Chiplet 能利用最合理的工艺满足数字、射频、模 拟、I/O 等不同模块的技术要求,把大规模的 SoC 按照功能分解为模块化的芯粒,在保持 较高性能的同时,大幅度降低了设计复杂程度,有效提高了芯片良率、集成度,降低芯片 的设计和制造成本,加速了芯片迭代速度。Chiplet 技术的兴起,拉动测试产业整体需求。在 CP 测试环节,因为 Chiplet 封装成本 高,为确保良率、降低成本,需要在封装前对每一颗芯片裸片进行 CP 测试,相较于 SoC, Chiplet 对芯片的 CP 测试需求按照芯片裸片数量成倍增加;在 FT 测试环节,随着 Chiplet 从 2D 逐渐发展到 2.5D、3D,测试的难度提升,简单测试机减少,复杂测试机增加。Chiplet 技术拉动了测试需求,半导体测试厂商有望迎来需求起量。
大趋势下的国产替代:芯片制造链从台系向内地转移
中国大陆正承接产业迁移,带动国内半导体测试产能扩张。自从上世纪 70 年代半导体产 业在美国形成规模以来,半导体产业沿着“美国→日本→韩国和中国台湾→中国大陆”的 顺序共经历了三次产业迁移。中国大陆凭借着劳动力成本、技术、人才等优势,完成了半 导体产业的原始积累。此外,受地缘政治等因素的影响,建立自主可控的产业链已成为当 前阶段的重要目标,特别是特种芯片及高端 AI 算力芯片制造链回迁迫在眉睫。半导体国 产化进程正持续加深,带动国内半导体测试新产能不断扩张。
国内晶圆厂及 IDM 厂商资本开支处于高位,扩产趋势明显,有望拉动整体测试需求。受产 业链转移趋势影响,国内晶圆厂及 IDM 厂商资本开支持续处于高位,正处于不断扩产的过 程。测试在产业链中的位置紧贴晶圆厂,伴随着晶圆制造产能的迁移,测试产能有望随之 向国内转移。根据中芯国际 2023 年报中给出的对于 2024 年的指引,资本开支较 2023 年 有望保持持平。展望未来,国内晶圆厂资本开支有望持续处于高位,与之配套的测试服务 产能有望迎来快速增长。

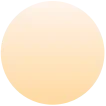
01.芯片封测

芯片封测是半导体生产过程的关键环节之一,包括芯片测试和芯片封装两个步骤。
芯片测试是在半导体制造的过程中对芯片进行严格的检测和测试,以验证芯片是否符合设计要求,包括数字、模拟、混合信号电路的测试等,并检查焊点的可靠性和连接强度。这一步是为了确保芯片的质量和稳定性。
芯片封装则是将测试完成的芯片进行封装,以便其被应用在各种设备中。封装过程涉及一系列工艺和技术,包括晶圆减薄、晶圆切割、光检查、芯片贴装等,封装后还要对封装工艺质量和代工质量进行测试,以保证芯片的稳定性和可靠性。

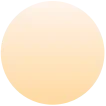
02.芯片封测的基本流程

芯片封测的基本流程主要包括封装和测试两大环节。
在封装环节,首先进行晶圆减薄,将刚出厂的晶圆进行背面减薄,达到封装需要的厚度。接着是晶圆切割,将晶圆切割成一个个独立的Dice,并对这些Dice进行清洗。然后,进行芯片粘接,即将芯片粘接在基板上,银浆固化以防止氧化,再进行引线焊接。完成这些步骤后,进行注塑,用EMC(塑封料)把产品封装起来,并加热硬化。随后,进行激光打字,在产品上刻上生产日期、批次等内容。紧接着是高温固化,以保护IC内部结构,消除内部应力。之后,去溢料,修剪边角。最后,进行电镀,提高导电性能,增强可焊接性。
在测试环节,主要包括功能测试和焊点可靠性测试等。功能测试是对芯片的功能进行测试,验证芯片是否符合设计要求。焊点可靠性测试则是对芯片焊点的可靠性进行测试,验证焊点的可靠性和连接强度。
常见的封测设备和工具
-
封装设备:封装设备主要用于将芯片封装在适当的封装体中,常见的封装设备有自动封装机、上胶机、压合机等。这些设备能够自动化完成芯片的封装过程,提高生产效率。
-
测试设备:测试设备用于对封装好的芯片进行测试,包括性能测试和功能测试。常见的测试设备有测试机、探针台、显微镜等。测试机能够对芯片进行电性能测试,探针台则用于对芯片进行物理连接和信号传输,显微镜则用于观察芯片的结构和缺陷。
-
测量工具:测量工具用于精确测量芯片的尺寸、形状和位置等参数。常见的测量工具有显微镜、千分尺、投影仪等。这些工具能够确保芯片的封装精度和质量。
此外,在芯片封测过程中,还需要使用一些辅助设备和工具,如清洗设备、烘烤设备、夹具、吸盘等。这些设备和工具在封装和测试过程中起着重要的作用,确保芯片能够正常工作和符合质量标准。
自动测试设备(ATE)
自动测试设备(ATE)是一种自动化系统,专门用于电气、热力和物理测试,无需人工直接干预。ATE的主要目的是加速测试过程、执行重复任务或增强测试系统的重复性和一致性。它广泛应用于半导体领域,对被测对象进行性能验证和故障诊断,具有工作效率高、操作简单、灵敏度高、精度高等优势。
ATE的主要工作流程是以计算机编程代替人工测试,基于测试程序控制仪器并对待测品进行输入和输出信号检测分析,从而判断待测品的性能是否符合要求。ATE的应用可以显著减少人工测试的成本和误差,提高测试效率和准确性。
随着技术的发展,ATE正朝着高度集成化、更高的测试速度以及适应5G和物联网(IoT)应用等方向发展。高度集成化的ATE测试座将整合更多的测试功能和自动化控制,以适应电子产品的复杂性和需求的增加。同时,ATE也需要具备更快的测试和数据传输速度,以满足更高的产能需求。
探针卡
探针卡(probe card)又称晶元探针卡,是晶圆测试厂广泛用于晶圆测试的关键接口,主要由PCB、探针、ring组成,根据不同需求,还可能有电子元件等。其功能是将探针卡上的探针直接与芯片上的焊垫或凸块直接接触,导出芯片讯号,再配合周边测试仪器与软件控制达到自动化量测晶圆的目的。探针卡的应用范围广泛,包括内存、逻辑、消费、驱动、通讯IC等科技产品的晶圆测试。
探针卡主要分为悬臂探针卡和垂直探针卡两类,广泛应用于集成电路、光电器件、传感器件、电子器件、LCD等测试领域,服务的产业涉及半导体、军工、航天、汽车电子、工业控制、消费类电子等。
在操作时,需要准备一支探针卡和一台测试电路板的仪器设备,并检查电路板是否有损坏或松动的部件。然后,根据测试需求在电路板上选择测试点,并将探针卡的探头连接到测试点。最后,在测试仪器上观察结果并记录。
探针卡对于前期测试的开发及后期量产测试的良率保证都非常重要,是晶圆制造过程中对制造成本影响相当大的重要制程。
03.封测技术的分类
封测技术是指将半导体芯片进行封装,并进行测试的过程,其分类可以从多个维度进行考察。
从测试目的和阶段来看,封装测试技术主要可以分为成品测试技术、封装材料测试技术以及封装失效分析技术。成品测试技术是在电子产品组装和封装后进行的最终测试,主要用于检测产品是否符合设计要求和规格要求,通常包括功能测试、信号测试、无损测试等。封装材料测试技术则主要用于测试封装过程中所使用的材料是否符合要求,涉及到材料的可靠性、耐久性、机械强度和导电性等方面。封装失效分析技术则是对封装过程中所发生的各种故障进行分析和诊断,确定故障原因和采取措施。
从测试手段和方法来看,常见的封装测试技术有人工目检(MVI)、在线测试(ICT)、自动光学测试(AOI)、自动X射线测试(AXI)以及飞针测试等。人工目检是一种用肉眼检查的方法,但在处理细间距芯片和焊接质量检查时,其效果可能并不理想。飞针测试则是以两根探针对器件加电来实现检测的方法,但随着器件的小型化和产品的高密度化,其不足也逐渐显现。ICT针床测试是一种广泛使用的测试技术,测试速度快,适合单一品种大批量的产品。自动光学检测(AOI)则是近几年兴起的一种检测方法,具有高效、准确的特点。
此外,根据封装形式和技术特点,还有系统级封装(SiP)和晶圆级封装(WLP)等先进封装测试技术。这些技术不仅提高了芯片的集成度和可靠性,还在尺寸、重量和功耗等方面取得了显著优势。
04.封测过程中的常见问题和挑战
封装问题:封装过程中可能出现的问题有焊接不良、封装裂纹、封装漏胶等。焊接不良可能表现为焊点未焊接、焊接不良或焊点短路等,影响芯片的电气性能。封装裂纹则可能由于材料的热膨胀系数不匹配或温度控制不当导致,影响封装的稳定性和可靠性。封装漏胶则与封装胶水不足或不均匀有关,可能导致封装器件出现漏胶现象。
测试问题:测试阶段的问题主要包括测试程序错误、测试环境干扰等。测试程序可能存在错误或不完整,导致测试结果不准确或无法正确评估芯片的性能。测试环境中可能存在干扰或噪声等因素,影响测试结果的准确性。此外,常见的测试挑战还包括漏气或渗漏、破裂、不均匀压力分布等问题,这些都可能导致测试结果不准确或测试失败。
操作和技术挑战:芯片封测过程中,操作技术不当也可能引发问题。例如,操作员可能未能正确安装密封部件,或者使用了不合适的密封材料,这些都可能导致密封性能不达标。此外,随着芯片尺寸的不断缩小和集成度的提高,对测试设备的精度和稳定性要求也越来越高,这增加了操作和技术上的难度。
环境与可靠性挑战:温度变化和材料膨胀等因素也可能对封装和测试过程造成影响。温度变化可能引起材料膨胀或收缩,导致密封件不再紧密。而材料膨胀则可能在高温和高压环境下导致密封材料破坏。

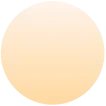
05.封装故障

-
焊接不良:
-
焊点裂缝:由于焊接过程中产生的热应力造成。
-
焊点虚焊:焊接温度或时间不足导致。
-
焊点短路:焊料流动不良或焊点位置偏移造成。
-
接触不良:
-
引脚接触不良:由引脚表面氧化、污染或引脚与接插件之间的接触不良造成。
-
引脚断裂:引脚材料缺陷或外力引起。
-
引脚过度磨损:长时间插拔或使用环境恶劣导致。
-
封装裂纹和漏胶:
-
由于封装材料选择不当、封装工艺参数不合适或环境因素(如温度变化、湿度等)的影响,可能导致封装体出现裂纹。
-
封装漏胶则可能与封装胶水的质量、涂覆工艺或固化过程有关。
-
机械损伤:
-
在封装、运输或安装过程中,芯片可能受到物理冲击、振动等机械应力的作用,导致封装体或内部结构受损。
-
材料问题:
-
封装材料的质量、成分和属性对封装质量有重要影响。例如,材料的热膨胀系数不匹配可能导致封装体在温度变化时产生应力,进而引发故障。


06.测试失败

-
芯片设计问题:设计缺陷是导致测试失败的重要原因之一。芯片设计中如果存在错误或不完善的地方,其功能或性能可能无法满足预期。设计上的不足可能导致芯片在测试阶段表现出不符合要求的行为,从而引发测试失败。
-
测试程序问题:测试程序是评估芯片性能的关键工具。如果测试程序存在错误或不完整,那么测试结果可能不准确或无法正确评估芯片的性能。测试程序的设计和优化是确保测试准确性和可靠性的重要环节。
-
环境因素:测试环境中的干扰或噪声等因素也可能对测试结果产生负面影响。这些环境因素可能干扰测试信号的准确性,导致测试结果与实际情况不符,从而引发测试失败。
为了降低测试失败的风险,可以采取以下措施:
-
在芯片设计阶段进行全面的验证和仿真,尽量避免设计缺陷的出现。
-
优化测试程序和方案,确保覆盖率和准确性,提高测试的可靠性。
-
加强测试环境的控制,减少干扰和噪声的影响,确保测试结果的准确性和可靠性。

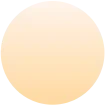
07.封测技术的发展趋势

封测技术的发展趋势呈现出多个方向,随着电子信息产业的快速发展和新兴领域的不断涌现,芯片封测市场需求持续增长,为封测技术的发展提供了广阔的空间。
随着物联网、智能家居等领域的兴起,对高可靠性集成电路的需求不断增加,因此,高可靠性封测方案的需求也在增长。这要求封测技术不断创新,以满足市场对高质量集成电路的需求。
先进封装技术将成为未来封测市场的主要增长点。在芯片制程技术进入“后摩尔时代”后,先进封装技术能在不单纯依靠芯片制程工艺实现突破的情况下,通过晶圆级封装和系统级封装,提高产品集成度和功能多样化,满足终端应用对芯片轻薄、低功耗、高性能的需求,同时大幅降低芯片成本。
随着新材料、新工艺的不断涌现,芯片封测技术将迎来更加广阔的发展空间。新材料和新工艺的应用将进一步提升封测技术的性能,降低制造成本,并推动产业向高端化、智能化发展。
原文始发于微信公众号(半导体工艺与设备):功率器件模块封装结构演进趋势