碳化硅衬底难加工的材料特性叠加其大尺寸化、超薄化的放大效应,给现有的加工技术带来了巨大的挑战,高效率、高质量的碳化硅衬底加工技术成了当下的研究热点.本文综述了碳化硅衬底机械磨抛加工技术和化学反应磨抛加工技术的研究进展,对比各类磨抛技术的特点,指出碳化硅衬底磨抛加工技术面临的挑战和发展趋势,以期为大尺寸碳化硅衬底的高质量、高效率、低成本加工提供新的思路和方法。
碳化硅相较于第一、二代半导体材料具有更优良的热学、电学性能,如宽禁带、高导热、高温度稳定 性和低介电常数等,这些优势使得以碳化硅为代表的宽禁带半导体材料广泛应用于高温、高频、高功率 以及抗辐射等极端工况.作为高性能微电子和光 电子器件制造的衬底基片,碳化硅衬底加工后的表 面、亚表面质量对器件的使用性能有着极为重要的影响,因此,其加工不仅要保证较高的面型精度和亚 纳米级的粗糙度,还要避免表面及亚表面损伤. 碳化硅的主要加工过程分为切割、磨削/研磨以及抛 光,其中磨削/研磨以及抛光这两道工序是决定碳化 硅衬底最终加工质量优劣的关键工序 . 由于碳化硅 被视为典型的硬脆性难加工材料,其加工过程面临 着效率低、成本高以及对环境不友好等问题.为了获得满足要求的碳化硅衬底,研究人员开发了多种精密磨抛加工技术,根据材料去除方式的不同可以分为以机械去除为主的机械磨抛技术,以及以化 学反应为主的化学反应磨抛技术 . 机械磨抛技术通 过磨粒的机械作用或叠加特种能量的机械辅助作用来达到快速去除材料并获得良好表面质量的目的, 化学反应磨抛技术先使衬底表面材料发生化学反 应,形成较软的变质层,再利用磨粒划擦去除以获得 亚纳米级粗糙度的表面质量 . 由于碳化硅晶体生长 技术的限制,难以获得如硅、蓝宝石等超大棒料晶体,故未来的碳化硅衬底将朝着大尺寸、超薄化的方 向发展,通过对磨抛加工技术的深入研究可以为其 高效率、高质量、低成本加工提供新的思路和方法.
本文以研究第三代半导体碳化硅衬底磨抛加工 技术为目的,综述了机械磨抛技术、化学反应磨抛技 术的进展. 根据去除机理的不同,划分并总结现有磨 抛技术的特点:传统机械磨抛拥有较高的材料去除 率,但是其加工质量较差,且损伤严重;而化学腐蚀 反应磨抛的加工质量较好,但是较低的材料去除率 是其亟待解决的难题;机械诱导反应磨抛以及特种 能量辅助机械磨抛能够兼顾加工质量及加工效率, 已经成为当下的研究热点之一.最后根据高质量、高 效率、低成本、绿色发展的要求,对未来大尺寸、超薄 化碳化硅衬底的磨抛加工技术进行了展望.
由于碳化硅具有极高的化学稳定性,沿用硅晶 圆的化学机械抛光方法难以获得较高的加工效率 . 因此,研究人员首先采用传统的机械去除方法以期 快速去除前道工序引入的损伤层,并降低表面粗糙度. 为了进一步提高加工效率和获得较高表面质 量,研究人员引入特种能量辅助机械磨抛加工.
1.1 传统机械磨抛技术
从磨料运动方式来看,传统机械磨抛技术经历了从游离磨料研磨到固结磨料磨削的发展过程,碳化硅衬底的磨抛技术也随之不断发展和进步.
传统的游离磨料研磨主要通过研磨盘、工件和磨粒三者之间的相互作用,达到材料去除的目的,但因磨粒分布不均匀、运动轨迹不可控,难以保证碳化硅衬底的形状精度和表面质量 . 研究人员使用 不同的磨料对碳化硅进行加工,发现金刚石磨料拥有较好的材料去除率,且Yu等发现研磨后的碳化 硅的表面形状精度有了明显的改善 .Yuan 等研究不同粒径金刚石的加工效果,他们发现当金刚石粒径为0.5 µm时,可以获得最佳表面粗糙度Ra=48.7 nm的 碳化硅表面,且材料去除率为3.18 µm/h. Pan等使用金刚石砂轮磨削碳化硅衬底,可以得到表面粗糙 度 Ra=12 nm,且晶圆整体厚度变化(Total Thickness Variation)<3 µm 的碳化硅衬底 . 固结磨料磨削通 过使用固结磨料磨盘或砂轮的方式,可以有效提高 磨粒利用率. 但是由于磨粒出刃高度不一致,碳化硅 表面会产生严重的划痕和表面、亚表面裂纹,加工后 表面质量难以满足抛光前的要求 . 研究人员通 过使用超细磨料砂轮,以纳米磨削方式对碳化硅进 行加工,可以获得 Ra=2 nm 左右的表面粗糙度 .Huo 等使用纳米磨削加工碳化硅,可以获得小于 1 µm 的平面度 . 虽然纳米磨削可以获得较低的表面粗糙 度,但是存在超细磨料砂轮制作成本高及制作难度大,且加工后仍然会存在亚微米深的裂纹、损伤层等问题,这些都是其亟待解决的难题. 作为高性能器件的载体,碳化硅衬底要求原子级的表面且无损伤层, 研磨及磨削加工后的表面需要进一步通过抛光进行加工.由于抛光使用的是柔性加工工具,在一定程度 上会破坏衬底平整度,所以对磨削加工后的翘曲度也有着较高的要求 . 研究人员使用纳米级的金 刚石磨粒对碳化硅衬底进行机械抛光,可以获得亚 纳米级的表面粗糙度,但是需要花费较长的时间及较高的成本 . 抛光后的表面损伤及粗糙度虽有所改善,但加工后表面仍然会存在划痕,难以满足衬底原 子级表面的要求.
典型机械磨抛技术的材料去除机理如图 1 所 示,Hx为相同时间内不同加工方式的材料去除深度. 纳米磨削使用的磨料一般为 W1-10的金刚石,其材料去除率高,且表面质量较好,但是超细砂轮造价高 导致加工成本较高,并且会残留亚微米深的损伤层 . 传统磨削使用的磨料一般为 W50-100 的金刚石,虽然磨料粒度要远高于纳米磨削时使用的磨料,但是由于传统磨削加工时,工具的转速过低,加工区域磨料线速度远低于纳米磨削中的线速度,所以其材料 去除率小于纳米磨削,且加工后表面质量较差,损伤层厚达微米级 .机械抛光使用的磨料一般为 W0.1-3 的金刚石磨料,加工后的表面质量较好,但存在划痕 和较浅的亚表面损伤层 . 研磨使用的磨料一般为 W0.5-20 的金刚石和碳化硅,它的材料去除率及表 面质量介于上述3种加工方法之间.
1.2 特种能量辅助机械磨抛技术
传统的机械磨抛技术可以实现对材料的高效去除,但是加工后较差的表面质量是当前急需优化的方向. 为了解决这一难题,国内外学者引入特种能量 来辅助机械磨抛加工,如图 2所示 .超声振动辅助磨削主要通过对主轴添加超声振动的方式辅助磨削;激光辅助加工通过激光照射碳化硅表面,达到降低其表面硬度的目的;电火花磨削通过磨粒的间歇性放电实现对材料的去除 . 特种能量辅助机械磨抛技术在保证较高磨抛加工效率的同时,获得表面质量良好的碳化硅衬底,为超精密抛光加工节约工序余量.
超声振动辅助磨削(Ultrasonic Vibration Assisted Grinding, UVAG)是一种新型的精密加工技术,具有 提高材料去除率、减小磨削力、提高加工精度和表面 显著优势 完整性等优点,特别是在硬脆材料精密加工中具有 .曹建国等研究了碳化硅的超声振动辅 助磨削,他们认为超声振动会导致材料去除量增加, 且有利于实现碳化硅衬底的塑性去除 .Li 等通过 超声振动磨削6H-SiC薄膜,可获得表面粗糙度低于 23 nm 的表面 . 振幅由超声电源的输出功率调节,但 加 工 过 程 中 的 实 际 振 动 振 幅 会 受 到 磨 削 力 的 影 响 ,因此Chen等提出一种在磨削过程中实时监 控实际振动幅度的方法,该方法不受工具旋转、冷却 液等外界因素的干扰和影响.
激光辅助加工(Laser Assisted Machining, LAM) 具有材料损伤小、热影响区小等优点. 通过激光预处 理,能降低碳化硅的硬度,从而提高材料去除率,由 于加工过程简单且效果显著,加工碳化硅等硬脆材 料有很好的应用前景 . Chen等用激光照射碳化硅切割片的表面,降低碳化硅的硬度,使得磨削加工时 的材料去除率得到了明显的提高 . Luo 等使用激 光辅助加工碳化硅,获得的表面粗糙度与传统磨削相比降低了 37%~40%,且亚表面损伤层厚度下降了 22%~50.6%. Kim等通过将CO2激光源与机械抛光 相结合,首次尝试在浆液环境中进行激光辅助抛光, 提高了材料去除率 . Abrego等通过激光辅助加工 可以使材料去除率相较于传统抛光提高 43%. 虽然 激光辅助加工的成本较高,但是可以显著提高加工 质量及加工效率,同时可以实现混合加工,极大缩短 加工时间并且减少加工步骤,是一种非常有前景的精密加工技术.
电火花磨削(Electrical discharge grinding, EDG) 是 通过石墨轮对工件的间歇放电实现材料的去 除 . Yan 等先使用金刚石作为工具电极进行碳 化硅的电火花加工,然后使用金刚石去除电火花加 工过程中形成的2~3 µm厚的重铸层,加工后的表面 粗糙度为 1.85 nm. 电火花加工后,表面会残留较厚 的再凝固层和热致微裂纹,为了去除凝固层以及微 裂纹,需要在电火花加工后进行多次长时间的抛光 处理,故抛光的经济、时间成本较高. 因此,如何减 小甚至消除电火花引起的凝固层及微裂纹是电火花 磨削亟待解决的难题.
1.3 小 结
传统机械磨抛技术拥有较高的材料去除率,但 较低的加工质量使得其只适用于充当超精密抛光的 前一道工序,快速去除切割引入的损伤层,控制表面 质量,为超精密抛光减少去除余量. 同时由于衬底翘 曲度会对超精密抛光过程产生负面影响,在衬底翘 曲度较大时,可能会导致衬底表面出现凹凸不平的 区域,影响最终的加工质量和精度. 所以在快速去除 的同时,还要保证较低的衬底翘曲度. 虽然引入特种 能场的方式可以提高机械磨抛加工的加工质量,但 同样难以获得满足质量要求的碳化硅衬底 . 通过对 特种能场加工机理的深入研究,并借助新型在线检 测技术对加工过程进行实时监控,可以有效提高机 械磨抛技术的加工质量 . 同时,新的自动化、智能化 设备的研发也有助于特种能场辅助机械磨抛技术向 高质量化的方向发展.
由于高质量的碳化硅衬底需要原子级的表面及 较高的面型精度,传统的机械磨抛技术难以获得满 足要求的碳化硅衬底 . 化学反应磨抛技术通过化学 腐蚀或者机械诱导的方式先使衬底表面材料变质钝 化,再利用磨粒划擦实现材料去除,可以获得亚纳米 级的表面粗糙度且减小甚至消除衬底的表面及亚表面损伤 . 根据化学反应产生的方式分为以化学腐蚀为主的反应磨抛技术以及以机械诱导为主的反应磨抛技术 . 以化学腐蚀为主的反应磨抛技术可以获得 质量较高的表面,但是其材料去除率较低;而以机械 诱导为主的反应磨抛技术可以在保证表面质量的同 时,拥有较高的材料去除率.
2.1 以化学腐蚀为主的反应磨抛技术
以化学腐蚀为主的反应磨抛技术的核心是通过 化学试剂或特种能场对碳化硅的表面进行氧化腐 蚀,从而形成较软的变质层,再通过磨粒划擦将变质 层去除. 这类反应磨抛技术以抛光加工为主,其中又细分为化学机械抛光 、电化学机械抛光、等 离子体辅助抛光 、紫外光辅助化学抛光等不 同类型的抛光方法.
2.1.1 化学机械抛光技术
目前业内最主流的化学腐蚀反应抛光技术是化 学 机 械 抛 光 技 术(Chemical Mechanical Polishing, CMP),化学机械抛光技术是一种在加工过程中利用 化学试剂腐蚀和磨粒机械去除复合的方法对衬底材 料进行超精密加工的反应抛光技术,能够获得超光 滑甚至无损伤的衬底表面 . 为了提高化学机械抛光 高化学作用两个方面进行了研究,如图 的材料去除率,研究者们分别从提高机械作用和提 3所示,通过 使用较硬的磨料可以有效提高机械作用;改变抛光 液的 pH 值或者加入氧化剂、催化剂可以提高化学 作用.
1)提高机械作用.Su等 使用AI2O3磨料对碳化 硅进行抛光,能够得到 0.36 µm/h 的材料去除率,是 使用SiO2磨料的2倍以上.Heydemann等使用金刚 石磨粒对碳化硅进行化学机械抛光,发现材料去除 率是只使用 SiO2磨料的 10 倍;当向 SiO2研磨液中同时加入金刚石磨料和 NaClO 氧化剂后,其材料去除 率提高了15倍,抛光后的表面粗糙度降低了6.28 nm. Lee 等使用含有 SiO2和金刚石磨粒的抛光液对碳 化硅进行化学机械抛光,获得表面粗糙度为 0.27 nm 的碳化硅,且材料去除率约为1.8 µm/h.
2)提高化学作用. Zhou等研究了pH值对CMP 中化学腐蚀速率的影响,他们发现较高的pH值可以 适当加快化学腐蚀速率进而提高材料去除率,在 55 ℃且pH值为11的情况下,能够获得0.2 µm/h的最 大材料去除率 . Aida 等研究酸碱性研磨液对抛光 碳化硅的影响,发现碱性适合抛光Si面,酸性适合抛 光C面. Nitta等发现添加胺之后的过氧化氢抛光液 的材料去除率提高了1.7倍,比只使用磨粒的抛光液 提高了8倍左右. 由于化学腐蚀速率对化学机械抛光 的材料去除率有重要影响,所以研究者们采取了一系 列方法来提高化学腐蚀的速率,如引入芬顿反应及催化剂辅助刻蚀技术. Kubota 等证实了芬顿反 应提高化学机械抛光中的化学反应速率的可行性 . Lu等在碳化硅的CMP加工中引入芬顿反应,加工 后获得表面粗糙度Ra为0.187 nm的原子级光滑表面, 材料去除率为0.154 µm/h. Hara等提出了催化剂辅助刻蚀技术(Catalyst Referred Etching, CARE)并且对 碳化硅进行了加工,其原理是碳化硅被强氧化剂氧化 为 SiO2,接着 SiO2与 HF 发生反应生成氟硅酸而被去 除,从而达到超精密加工目的,加工后的表面平坦无 划痕,且表面粗糙度只有 0.076 nm,材料去除率为 0.1~0.2 µm/h. Pan 等研究了不同催化剂的加工效 果,结果表明当催化剂为氢氧化钾时,加工后的表面 粗糙度为0.174 nm,材料去除率为0.105 µm/h.
从碳化硅的化学机械抛光研究中可以看出,通 过提高加工中的机械作用以及化学作用都可以提高 加工效率,也取得一定效果. 化学机械抛光中最主要 的优化方向是平衡化学反应的速率以及机械去除的 速率. 当化学反应的速率高于机械去除的速率时,就 无法及时去除化学反应生成的软质 SiO2层,加工后 碳化硅表面会残留一定厚度且成分为 SiO2的损伤 层;当机械去除的速率高于化学反应的速率时,碳化 硅表面还来不及形成软质 SiO2层就与磨料接触,导 致材料去除率过低. 因此,平衡化学反应速率和机械 去除速率能够同时获得较高的表面质量以及材料去除率.
2.1.2 特种能场辅助化学机械抛光技术
化学机械抛光技术能够获得较高的表面质量, 但是较低的材料去除率以及对环境的不友好是其亟 待解决的难题 . 通过添加特种能场的方式能够替代 化学试剂对碳化硅表面进行氧化腐蚀,同时降低化 学试剂对环境的影响. 如图4所示,电化学机械抛光 技术通过阳极氧化的方式提高化学腐蚀速率;等离 子体辅助抛光技术通过等离子体对碳化硅表面进行 氧化改性;紫外光辅助化学机械抛光技术通过紫外 光及催化剂对碳化硅表面进行氧化腐蚀.
有研究者提出在化学机械抛光中引入电场,即 电 化 学 机 械 抛 光 技 术(Electrochemical Mechanical Polishing, ECMP). 该方法是利用阳极氧化的方式提 高化学腐蚀速率,能够有效地提高加工效率,并获得 光滑表面 . Li等研究了电流密度对电化学机械抛 光的影响,他们发现当电流密度超过 20 mA/cm2 时, 阳极氧化和机械去除能够更好地适配,从而提高加 工效率 . Yang 等提出无抛光液的电化学机械抛 光,获得了无划痕的碳化硅表面,且表面粗糙度下降 至 1.352 nm. Chen 等对阳极氧化的条件进行了进 一步的探究,他们发现当 pH=7 时,溶液会有更好的 氧化效果. Murata等提出一种使用聚氨酯-氧化铈 核壳颗粒的无抛光垫的电化学机械加工方法,虽然 抛光后表面的划痕没有完全消除,但是材料去除率 可达 3~4 µm/h. Yang等 提出了一种三步无抛光液 的电化学机械抛光工艺,可以获得表面粗糙度为 0.11 nm 的 碳 化 硅 表 面 且 材 料 去 除 率 可 以 达 到11 µm/h. 电化学机械抛光是一种很有潜力的加工方 式,利用绿色电能代替了化学试剂,减少了对环境的 污染,同时加工效率也有明显的改善. 由于目前电化 学机械抛光都聚焦在小尺寸的碳化硅加工上,随着 装备及自动化技术的发展,未来碳化硅的电化学机 械抛光将朝着大尺寸、全局平坦化、自动化的方向发展.
Yamamura 等提出了一种利用常压等离子体 辐照加工材料的新方法,即等离子体辅助抛光技术 (Plasma Assisted Polishing, PAP),其原理是使用等 离子体对碳化硅衬底进行辐照,通过羟基自由基来 氧化碳化硅衬底表面,形成软质 SiO2,再通过软磨料 机械去除 SiO2变质层,等离子体辐射的表面氧化改 性和机械去除相互交替进行,从而达到材料去除的 目的. Yamamura等使用氦气等离子体对碳化硅进 行辐照,通过纳米压痕试验表明,辐照后碳化硅硬度 从 37.4 GPa降低至 4.5 GPa,然后再使用 CeO2软磨料 抛光,获得表面粗糙度为0.1 nm的超光滑、无划痕的 原子级表面 . Deng等使用氦气与水蒸气的等离子 体辐照碳化硅衬底,实验证明当氦气中水蒸气浓度 在 0.022% 时,等离子体氧化速率为最高,且当抛光 速率大于氧化速率时,能够获得阶梯宽度均匀的原 子表面阶梯结构. 目前,从等离子体辅助抛光技术的 发展来看,高效率、高精度、低能耗、智能化已成为该 技术的发展趋势. 另外,开发更先进的在线检测技术 也将成为研究热点,以实现对加工量的准确控制,达 到精确去除的目的.
研究者们将紫外光催化反应运用到碳化硅的化 学机械抛光的过程中,形成了紫外光辅助化学机械 抛光技术(Ultraviolet Assisted CMP, UV-CMP). 通过 紫外光照射光催化剂产生光催化反应,生成羟基自 由基,羟基自由基将碳化硅表面氧化成软质SiO2,再 通过磨粒划擦去除 SiO2变质层 . 紫外光催化反应和 磨粒划擦去除相互交替进行,能获得超平坦、超光 滑、无损伤的原子级表面 . Ishikawa等探究紫外光 辅助抛光的可行性,发现在室温下 TiO2的光催化作 用使得碳化硅表面生成二氧化硅 .Tanaka 等人研究在紫外光下使用不同催化剂对碳化硅的抛光影 响,结果表明,当催化剂为TiO2时,能够获得无损伤、 超光滑的原子级表面,且材料去除率为 0.313 µm/h. Yan等研究影响紫外光催化反应速率和抛光效果 各个因素,发现H2O2浓度对反应速率的影响最大,光 照强度的影响最小,在最佳参数下进行光催化辅助 化学机械抛光,最佳的表面粗糙度为 0.423 nm,材料 去除率为 0.107 µm/h. 寻找新的催化效率更高的光 催化剂将是提高 UV-CMP 材料去除率的重要手段, 未来将进一步研究光催化剂以及反应物的最佳摩尔 比,以及增强光催化活性的新方法,进而提高磨抛加 工的效率.
2.2 以机械诱导为主的反应磨抛技术
以化学腐蚀为主的反应磨抛技术可以获得理想 的碳化硅衬底,但是较低的效率以及对环境的不友 好都是其亟须解决的问题 . 因此研究人员提出在加 工过程中通过机械力划擦诱导化学反应,达到兼顾 效率以及表面质量的目的.
2.2.1 磨粒划擦诱导碳化硅水反应的反应磨抛技术
Lu等提出了一种用于超精密加工的绿色、高 效、半固结的磨料工具——SG 抛光垫,在仅使用蒸 馏水作为冷却液的情况下利用该工具可以获得超光 滑、无划痕、几乎无表面损伤的碳化硅衬底表面 . 这 一技术被称作溶胶凝胶抛光技术,这是一种新型的 绿色高效抛光技术,该技术借助软质基体所拥有的 柔性特点,实现了磨粒的“容没”效应. “容没”效应是 指在抛光加工过程中磨粒接触到加工表面时,由于 软质基体的存在,较为突出的磨粒可以产生回弹,进 而保证表层磨粒能够近似在同一水平面内对工件进 行加工,从而获得均匀的材料去除,以达到更好的抛 光效果,是一种非常有潜力的绿色高效抛光技术 . Luo 等使用金刚石和氧化铝磨料的半固结和固结 抛光垫进行了对比试验,发现固结磨料抛光工具的 材料去除尺度不均匀,从几纳米到几百纳米不等,很 难保持表面的完整性;而使用半固结抛光垫却能够 获得具有亚纳米级的光滑无划痕表面,同时在加工 后的表面上发现了纳米级厚度的非晶型SiO2.
为了研究非晶 SiO2的产生原因,罗求发对碳化硅的磨粒抛光去除机理进行了研究,发现在磨粒 与衬底表面的机械摩擦作用下,碳化硅表面生成了 非晶 SiO2. 通过进一步研究发现,该现象本质为磨粒 划 擦 诱 导 了 碳 化 硅 与 水 发 生 了 化 学 反 应 . Cheng 等对碳化硅与水的摩擦化学反应机理进行了深入 研究. 发现在纳米尺度中,碳化硅衬底表面在金刚石 压头的反复机械作用下被诱导成非晶化的碳化硅, 然后非晶化的碳化硅再和水反应生成 SiO2;控制碳 化硅与水反应的主要因素是载荷和接触状态,其次是速度和温度 . 这一研究阐述了碳化硅与水反应的 条件,对其进行合理的利用,可以使碳化硅衬底的加 工效率和表面质量得到显著的提升.
在碳化硅衬底的减薄加工过程中有效地应用碳 化硅与水的反应可以合理避免裂纹的产生,进而提 高碳化硅衬底的表面质量. 同时,利用半固结磨料磨 削的方式可以有效地解决加工效率和加工质量不能 兼顾的问题 .如图 5所示,在碳化硅衬底的减薄加工 中通过控制磨粒的“容没”效应使得突出高度分别为 H1~H4的磨粒保持在同一高度H5上,进而通过磨粒划 擦诱导碳化硅表面生成非晶碳化硅,然后非晶碳化 硅与水发生反应生成软质 SiO2,再通过磨粒划擦去 除 SiO2变质层,可以有效提高加工后碳化硅衬底的 表面质量.
2.2.2 金属摩擦诱导反应磨削技术
由于碳化硅具有超高的硬度,它经常被当作磨 料来加工金属等材料 . 但是在加工黑色金属时碳化 硅却有着异常的表现,它在加工过程中的磨损非常 大,这也直接导致了它不适用于加工黑色金属,针对 这 一 问 题 ,研 究 人 员 对 其 磨 损 原 理 进 行 了 研 究 . Komanduri 等对碳化硅在钴基高温合金上进行了 高速、低进给速度下的模拟磨削磨损试验,发现碳化 硅在高温下分解,Si 和 C 原子扩散到金属中形成金 属硅化物和不稳定的金属碳化物,在冷却过程中逐 渐分解 . Duwell 等报道碳化硅与铁反应生成铁硅化物. 前人的研究表明,纯金属可以与碳化硅在一定 条件下发生化学反应,因此将纯金属摩擦化学原理 应用于单晶碳化硅的加工在理论上是可行的.
基于此,Wu等研究了纯金属(铁和镍)对单晶 碳化硅的高速摩擦去除行为,研究表明碳化硅衬底 的C面获得了近乎无损伤的表面、亚表面,而碳化硅 衬底的Si面存在裂纹、位错、层错和晶格畸变等晶体 缺陷. 用铁摩擦碳化硅衬底的C面,其材料去除率可 达330 µm/h. 用纯镍摩擦碳化硅衬底的Si面,可获得 534 µm/h 的材料去除率 . 硅化物以及氧化物的形成 表明,碳化硅的 C 面和 Si 面去除均以金属摩擦诱导 化学作用为主 . 在反应变质层的不断生成及去除的 循环过程中,实现碳化硅的高速去除,纯金属摩擦诱 导碳化硅反应的材料去除机理如图6所示.
用金属摩擦诱导反应磨削碳化硅的方法少有人 研究,这是一种在碳化硅衬底磨抛和碳化硅芯片减 薄加工中具有巨大潜力的高效加工方法 . 由于目前 金属摩擦诱导反应磨削还聚焦在小尺寸的碳化硅加 工上,未来将朝着大尺寸、全局平坦化的方向发展, 同时提高金属的自锐性以及对加工过程的温度控制 也是保证加工表面质量的关键因素.
2.3 小 结
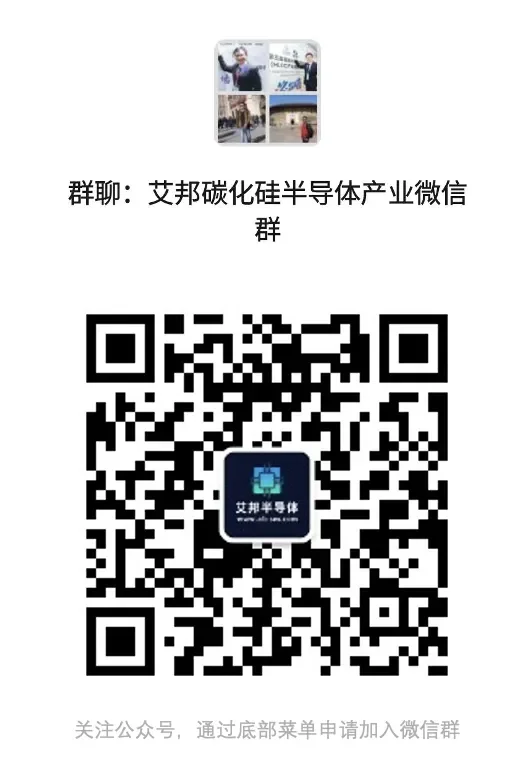
由于碳化硅晶体难以长成长条状的晶棒,所以 碳化硅晶体主要朝着大尺寸的晶锭方向突破,大尺 寸、超薄化的碳化硅衬底磨抛加工将是未来的研究 热点,如图 7所示,如何兼顾大尺寸碳化硅衬底的加 工效率和加工质量将成为关键. 目前,主要是通过单 面磨削和化学机械抛光的方式实现大尺寸碳化硅衬 底的磨抛加工,但是较低的良品率以及加工效率是 其亟待解决的难题 . 通过对现有碳化硅衬底磨抛技 术的总结及分析,未来碳化硅衬底磨抛加工技术的 发展将集中在工艺参数的优化、新磨料及抛光液的 研究、加工设备的自动化和智能化发展、环保加工方 法的开发、多尺度磨抛加工以及跨学科研究等方面.
1)大尺寸衬底磨抛加工工艺优化:通过试验以及仿真等手段,探讨大尺寸碳化硅衬底磨抛加工过 程中各个参数对加工结果的影响,并对其中的关键 参数进行控制以及优化,以期找到最合适的加工参 数,实现高效率、高质量、低成本加工.
2)研究新型磨料及抛光液:磨料及抛光液是影 响碳化硅衬底加工效率以及加工质量的关键因素 . 未来,研究人员将致力于研究和寻找新型的磨料以 及抛光液,以期实现磨料、抛光液与碳化硅的快速反 应,提高加工效率,并降低表面粗糙度.
3)研发智能化及自动化加工设备:借助现代计算机技术和人工智能技术,开发智能化和自动化的 加工设备,通过实时数据监测和分析,实现磨抛加工 过程中参数的实时控制和优化,提高加工效率和加 工质量.
4)开发新的加工方法:碳化硅衬底的磨抛加工 过程中会产生大量对环境不友好的废料、废水,探索 新的磨抛加工技术,如等离子刻蚀抛光技术、激光磨 抛技术等,可以有效减少对环境的影响,同时满足不 同场景的应用需求.
5)多尺度磨抛技术:目前碳化硅衬底需经过粗 磨、精磨、抛光等一系列加工步骤后才能得到理想的 表面质量,烦琐的加工步骤严重影响了加工效率以 及加工质量. 针对不同尺度的表面缺陷,科研人员将 研究多尺度磨抛技术,通过整合多种不同磨抛技术, 以实现从粗糙到光洁的磨抛一体化加工过程,减少 加工步骤的同时,获得高质量的碳化硅衬底.
6)跨学科研究:碳化硅衬底的磨抛加工技术涉 及多个学科领域,如材料科学、化学、力学等. 加强各 学科之间的交流,促进学科交叉融合,推动碳化硅衬 底磨抛技术的创新发展.
本文阐述了碳化硅衬底磨抛技术的研究进展与 发展趋势 . 碳化硅衬底磨抛技术的发展受到高性能 器件质量需求的牵引,同时也带动了碳化硅器件性 能的提升 . 由于机械磨抛技术主要依靠硬质磨粒划擦去除,所以难以获得满足表面质量的碳化硅衬底, 因此如何提高机械磨抛技术的加工质量将成为未来 的研究热点之一 . 化学腐蚀和机械诱导反应是化学 反应磨抛技术的核心,为了降低碳化硅磨抛加工过 程中的时间、经济成本,对化学腐蚀和机械诱导反应 的速率提出了更高的要求,同时化学反应速率和机 械去除速率的平衡是表面质量的重要影响因素 . 在 未来的研究中,需要优化大尺寸衬底磨抛加工中的 工艺参数和磨抛工具;开发新型超精密磨抛技术;研 发自动化、智能化的加工设备;实现碳化硅衬底加工 的磨抛一体化.
来源:湖南大学学报(自然科学版) 作者:罗求发 1,3†,陈杰铭 1,程志豪 1,陆静 1,2 (1. 华侨大学 制造工程研究院,福建 厦门 361021;
2. 华侨大学 脆性材料产品智能制造技术国家地方联合工程研究中心,福建 厦门 361021;
3. 高性能工具全国重点实验室,福建 厦门 361021)
声明:我们尊重原创,也注重分享;文字、图片版权归原作者所有。如有侵犯您的权益请及时联系,我们将第一时间删除,谢谢!
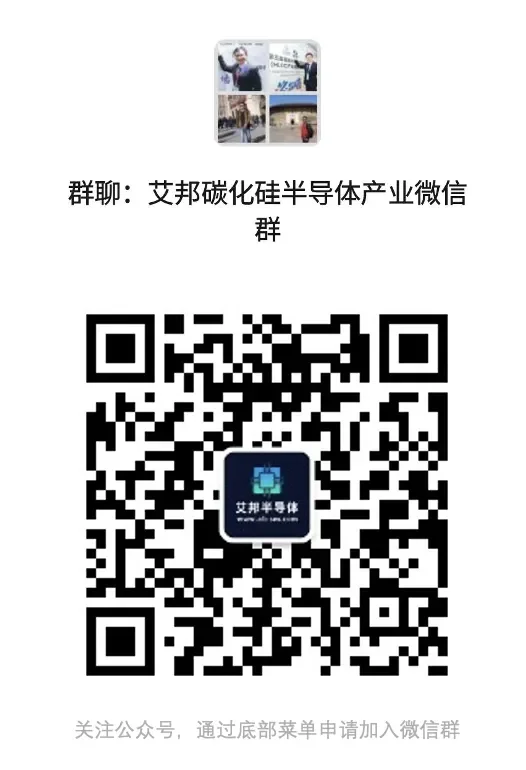
推荐活动:
01
会议议题
|
|
|
|
|
|
|
|
|
|
|
|
|
|
|
|
|
|
|
|
|
|
|
|
|
|
|
|
|
|
|
|
|
|
|
|
|
|
|
|
|
|
|
|
|
|
|
|
|
|
|
|
|
|
|
|
|
|
|
|
|
|
|
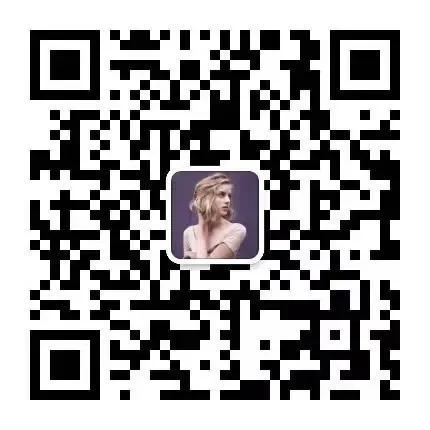
02
拟邀企业
-
高纯碳粉、硅粉、碳化硅粉末、坩埚、籽晶等材料企业; -
晶锭、衬底、外延、晶圆等产品企业; -
碳化硅晶体、外延生长等设备企业; -
金刚石线切割、砂浆线切割、激光切割等切割设备企业; -
碳化硅磨削、研磨、抛光和清洗及耗材等企业; -
检测、退火、减薄、沉积、离子注入等其他设备企业; -
高校、科研院所、行业机构等;
03
报名方式
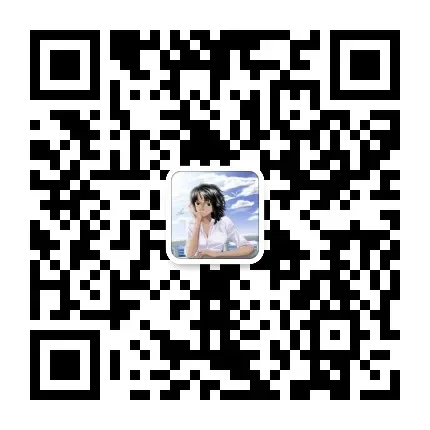
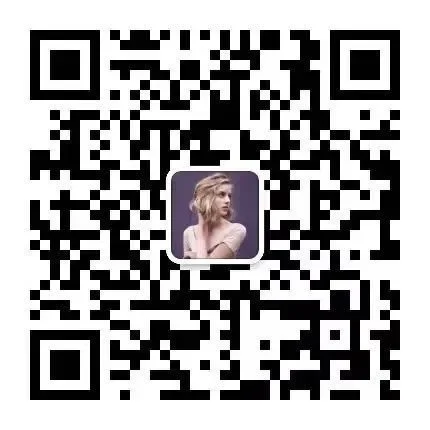
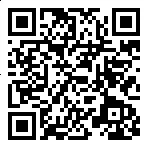
04
收费标准
|
|
|
|
|
|
|
|
|
|
|
|
|
|
|
05
赞助方案

原文始发于微信公众号(艾邦半导体网):碳化硅衬底磨抛加工技术的研究进展与发展趋势