英特尔公司的先进封装之TCB工艺及设备详述
查理
本文主要参考文献为:Thermo-compression Bonding for Fine-pitch Copper-pillar Flip-chip Interconnect – Tool Features as Enablers of Unique Technology
- 前言
如前文所述,封装路线的方向一直在向高性能轻薄化演进,为封装行业带来了全新的挑战和机遇。英特尔公司选择了基于基板(Substrate)的TCB(Thermal Compression Bonding 热压键合)工艺以替代传统的回流焊(Reflow)。该设备为英特尔和ASMPT公司联合开发,并于2014年导入量产,该设备有着极高的加工精度及丰富的可扩展性,不但可用于基板级封装,还可用于晶圆级封装,这就为英特尔在之后数年推出EMIB,Foveros等先进封装方式打下了扎实基础。
图1. 英特尔的Co-EMIB MCP (Multi-Chip-Package)封装产品
图2 英特尔的Foveros封装(芯片堆叠工艺)
我们将会先从英特尔为什么要引入TCB,从它前一代的技术回流焊遇到了什么样的挑战开始,然后介绍TCB的工艺细节,设备细节以及量产应用中的优化。最后再谈谈笔者自己的看法。
- 回流焊工艺及其挑战回顾
典型的倒装回流焊如图3所示:将芯片上的BUMP先浸蘸助焊剂,并贴在基板上。在进入回流炉前,助焊剂的粘性可将芯片软性固定,以防止其位置偏移,之后进入回流炉。在特定的升温降温(温度曲线如图4)下,凸点焊球会熔化为液态,在润湿铜微柱的过程中基于表面张力使得芯片回流对位,最后在降温作用下变成固相连接。
图3 芯片贴装流程 Flux Film: 助焊剂层,Flux Pot: 助焊剂容器,Flux Dipping: 助焊剂浸蘸, Position Flip chip on the substrate: 将芯片倒置对准基板上, Place Flip chip onto substrate: 将芯片放置于基板上,Reflow:回流焊,Flip chip soldering completed: 完成芯片倒装焊
图4 标准的回流焊曲线
- TCB 工艺介绍
但是由于超薄产品的引入,回流焊的缺陷率就开始增加如图5所示:翘起,非接触性断开,局部桥接等。回流焊的另外一个不足在于,芯片的位置容易发生偏移,一是料盘/载具在传输过程中受震动影响,二是回流过程中芯片的自由偏移。焊接凸点间距(Pitch)越小,芯片尺寸越大,则偏移失效越严重。
图5 回流焊流程中的各种缺陷
正是由于以上回流焊中的缺陷率越来越高,英特尔引入了TCB工艺。具体流程为:1, 基板(Substrate)在涂覆Flux后,被真空吸附固定在定制的加热板上。2,贴片头(BondHead)吸起芯片(Die),芯片在真空吸附下平整的贴合吸头(Nozzle)之下。3,光学相机辅助定位,基板所在的解热板位置微移,与芯片完成对位。4,BondHead向下运动,直到接触到基板的时候停止。5,Bondhead加载一个压应力,同时芯片会被快速加热直至锡球熔化温度。6,在锡球熔化的一刻,BondHead会将芯片继续向下走微小的距离,以确保所有的凸点能够连接。7,芯片在该高度保持数秒,确保锡球完全熔化浸润芯片和基板上的连接点。8,之后在熔融状态下,BondHead向上提升一定的高度,以得到预期的焊接高度。9,最后,BondHead快速降温,锡焊变为固相。Bondhead释放真空,回到待机位置。
在整个过程中,TCB会实时监测BondHead的温度(Temperature),吸头的应力( Bond Force)和Z方向的位移 (Bond Head Z Postion),其曲线如图6所示。整个焊接过程不超过4秒。
图6 TCB 焊接过程中曲线图
在TCB焊接过程中,锡球(Solder Ball)由固态转变为液态的一步非常关键,会相应触发BondHead由应力控制转为位置控制。另外一个有趣的现象就是锡球液化后的表面张力的影响,在压力曲线上会产生负值。由于该效应比较微弱,很容易与其他失效混淆,增加了信号识别难度。
-
TCB设备细节详述
TCB 设备外观
TCB设备的心脏是贴片头(Bond Head),由线性伺服马达(Linear Servo Motor)驱动空气轴承(Air Bearing)运动,如图7所示。有赖于高精度的伺服系统以及无摩擦的空气轴承导轨,垂直方向的运动精度可以控制在1um以内,从而实现锡球熔化过程下的微移动的精准控制。
贴片头配备了应力控制单元(Force Sensor),快速升降温脉冲加热器(Pulse Heater),还配备了一套主动倾斜控制系统(Active Tip Tilt,专利号US8387851B1)。
主动倾斜控制系统(Active Tip Tilt)可以精确调节脉冲加热器的共面度,使其与基板(Substrate)所在的加热板(Hot Pedestal)的表面完美贴合,在22mm x 33mm的区域内,可使上下两个平面共面间距不超过3um,几乎可以消除芯片翘起相关的失效。
压力传感器(Force Sensor)与压力传动方向同步,可实时监测贴片头在垂直方向运动中的应力反馈,从而得知芯片在贴片过程中的受压状态。线性伺服马达驱动可提供贴片头超过10N的贴片压力,压力伺服控制反馈系统可提供0.05N压力控制精度。
脉冲加热器(Pulse Heater)可提供每秒超过100度的升温速率,以及超过50度/秒的降温速度,这样从约400度(贴片过程中的最高温度)降到待机150度只需5秒左右。快速升温降温能力可以避免过多的热量持续加载给基板,并且显著缩短贴片所需时间。
加热单元中的组件得到充分工程优化,有良好的温度均一性,以及100度/秒的升温速率下,在22mm x 33mm区域内加热块表面的温度差异不超过10度。由此保证了芯片和基板的接触面锡球可以同步熔化。
贴片头使用的芯片吸头(Nozzle)为片状,尺寸与芯片尺寸匹配,材质为单晶,有极佳的导热性能,内有真空通道,可以将芯片牢牢吸附固定,且芯片吸头可以自动更换,可实现同一个基板贴装若干尺寸不同的芯片。
图7,焊接装置示意图(显示贴片头到焊接平台堆叠细节)
涂覆有液态助焊剂(Flux)的基板真空固定在加热板(Pedestal)上,加热板所在的平台(Bond Stage)坐落在空气轴承之上,在线性伺服马达驱动下进行无摩擦的水平移动。加热板最高可被加热到200度,在基板的贴片过程中可以精准控制基板的温度。芯片和基板通过上下同轴的高分辨率的相机系统对位(Up Looking and Down Looking Optics),该相机系统是热控设计,可避免图像因高温畸变,如图8所示。高精度的相机,以及无摩擦气垫运动的基板平台,保证了芯片和基板的极小的水平位置偏差,22mm x 33mm的芯片的偏移可小于2.5um且满足Cpk 1.33。
图8,焊接装置示意图(显示平台和设备内腔)
贴片头,光学相机板以及真空加热板都位于密闭的腔体内,如图8所示。冷却板(Cooling Plate)将整个腔体分为上方的大的惰性气体腔(Macro Inter Chamber)和小的惰性气体腔(Micro Inert Chamber),冷却板的正中央有一个开孔,贴片头的芯片通过此开孔与基板结合。冷却板可以防止下方大尺寸的加热板的热量传递到上方腔体,以避免影响贴片头和光学相机板的功能。芯片转移臂把芯片转运到冷却板的中央开孔处,之后贴片头向下运动将芯片吸起,芯片转移臂复位后,贴片头进一步向下运动,穿过中央开孔,将芯片贴置于基板上。上方密封腔充满了氮气(N2),将氧气的浓度控制在100ppm以下,以防止芯片在加热过程中的氧化。同时下方密封腔也有氮气气流,氧气的浓度同样控制在100ppm以下,以保护基板在加热过程中不被氧化。
图9,共面性测量
基板加热板(Pedestal)和贴片头的加热体(heater)的下表面之间的共面性是通过一对高精度的电容型传感器(Capacitive Sensors)测量的,该测量系统申请了专利(专利号:US8875979B2),如图9所示。电容传感器内置于光学相机板之上,可随着相机板以在贴片头和加热板之间水平移动。上下传感器成对同步工作,分别测量上方到贴片头的距离和下方到加热板的距离,两个距离之和为贴片头和加热板点对点的距离。随着水平方向的移动,可测量整个共面性。实际应用中,取芯片所在区域的4个角落(A,B,C,D)进行测量,用4个间距的最大差值来衡量共面度。贴片头的主动倾斜系统可将贴片头适度倾斜,使贴片头与下方加热板平行,满足微米级的共面度,这样芯片和基板之间的整体距离可以达到一致。
- 量产(HVM)过程中控制贴片质量的要素及优化
如图10为TCB封装的产品凸点锡焊键合的剖面图,芯片-基板间距控制良好,焊接过程不超过4秒。
图10,TCB焊接剖面图
基板和芯片将赋予不同的加热温度,以减少两者的膨胀效应差距。基板主要由数层有机材料构成,其翘曲效应受温度的变化影响较大,而芯片的形变则显著低于基板。基板的加热温度保持在较低的程度(如140度左右),而芯片则在脉冲加热器的作用下快速加热(超过100度/秒)和快速降温(超过50度/秒),这样可以显著减少热量传导给基板,贴片过程中基板可持续保持在较低的温度而不会过度膨胀。
其他一些有助于贴片质量的工艺优化:1. 在芯片与基板对位之前,芯片已经被加热到待机温度(约220度);2. 对位光学相机是热控设计的,可以保证高温测量的精度;3. 基板加热板的真空通路系统与基板有着良好的图案匹配度,基板在加热状态下可适度软化,在强力真空作用下贴合更平整,共面度更高。
TCB贴片头垂直方向选用了ZERODUR光栅尺,以提供高精度的垂直位置控制,从而能够精准的识别到锡球固液相变以及随后的精细位移控制。贴片头与基板加热板的热膨胀校准,用以补偿贴片头的垂直移动距离,从而更进一步提高精度,尤其是在固液相变以及锡液界面收缩过程中。每颗芯片在贴装过程中都会检测共面度,并反馈给贴片头主动倾斜补偿,以满足3um的共面度。在芯片和基板之间的锡焊完全固化前,提前释放真空吸附的芯片也可导致芯片翘起失效。适当增加贴片头的等待时间可以有效避免该失效。另外一种替代方法,即通过压力传感器的信号监测锡焊固化。冷却过程中,锡焊固化会将贴片头向下牵扯,表现为张力信号的增加。
- 量产中的工艺过程控制
为了满足可靠量产的需要,不同的TCB之间的输入输出经过校准后,其性能可都到一致性匹配。这样生产同一个产品时,所有的TCB设备会下载相同的工艺参数,不需要针对某一台TCB设备再单独设置。应用PCS(过程控制系统)监测重要的工艺指标参数。如果指标参数与目标值严重背离(如贴片头的压力,高度和温度等),PCS系统会将设备自动停止,并指导操作员做出相应的响应。PCS系统之外还集成了统计分析能力,可以反映每台设备的性能趋向,用于决定是否触发设备维护。充分利用强大的日志文件。贴片过程中的日志文件可以有效反映生产过程中的各种缺陷,如外来异物,助焊剂不足等等(如图11,图12所示),方便操作人员及时定位失效原因并给予修复。
图11异常焊接记录显示当出现其它物质时的曲线图
图12异常焊接记录显示当出现助焊剂不足时的曲线图
写在最后,英特尔公司采用的全新的TCB技术让人眼前一亮,在封装领域匹配了晶圆设备的性能。然而该工艺的特点以及精密的部件注定其成本不会低廉,维护诸多不易,应用场景较为苛刻。相信随着ASMPT公司对该设备的进一步优化且简化,并深度客户定制,业界采用该技术用于量产的公司会越来越多。
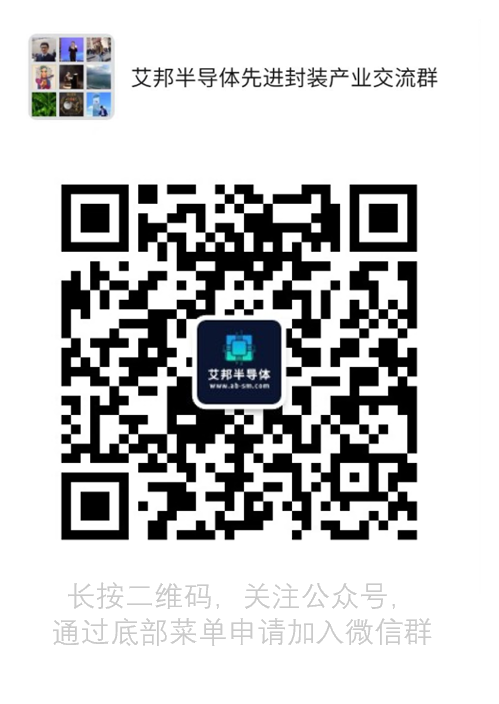