第3代半导体一般指禁带宽度大于2.2e V的半导体材料,也称为宽禁带半导体材料。半导体产业发展大致分为3个阶段,以硅(Si)为代表的通常称为第1代半导体材料;以砷化镓为代表的称为第2代半导体材料,已得到广泛应用;而以碳化硅(SiC)和氮化镓(GaN)、氧化锌(ZnO)、金刚石等宽禁带为代表的第3代半导体材料,由于其较第1代、第2代材料具有明显的优势,近年来得到了快速发展。
SiC、GaN、ZnO等第3代半导体具有更宽的禁带宽度、更高的导热率、更高的抗辐射能力、更大的电子饱和漂移速率等特性,更适合制作大功率电子器件。而SiC以其独特的排列结构,在材料综合性能、产品技术成熟度及产业化发展等方面都凸显出相对较高优势,具有高临界击穿电场、高电子迁移率等特性,与GaN相比更适合制作功率器件,且已在新能源汽车、风电、光伏太阳能发电和LED照明等领域得到广泛应用,如图1所示。
然而,随着第3代半导体SiC功率器件集成度和功率密度的明显提高,相应工作产生的热量急剧增加。因此,电子封装系统的散热问题已成为影响其性能和寿命的关键,要有效解决器件的散热问题,必须选择高导热的基板材料。据统计,由热引起的大功率器件失效高达55%。不仅如此,在新能源汽车、现代交通轨道等领域,大功率器件使用过程中还需要考虑颠簸、震动等复杂应用条件,这对基板等材料机械力学性能和可靠性提出了更高要求。
综合考虑,先进陶瓷材料以其具备高强度、高导热、耐高温、高耐磨性、抗氧化、热膨胀系数低和抗热震等热、力性能,同时具有较好的气密性,可隔离水汽、氧气和灰尘等特点,成为大功率半导体器件基板的最佳材料,被广泛应用到功率集成电路中。
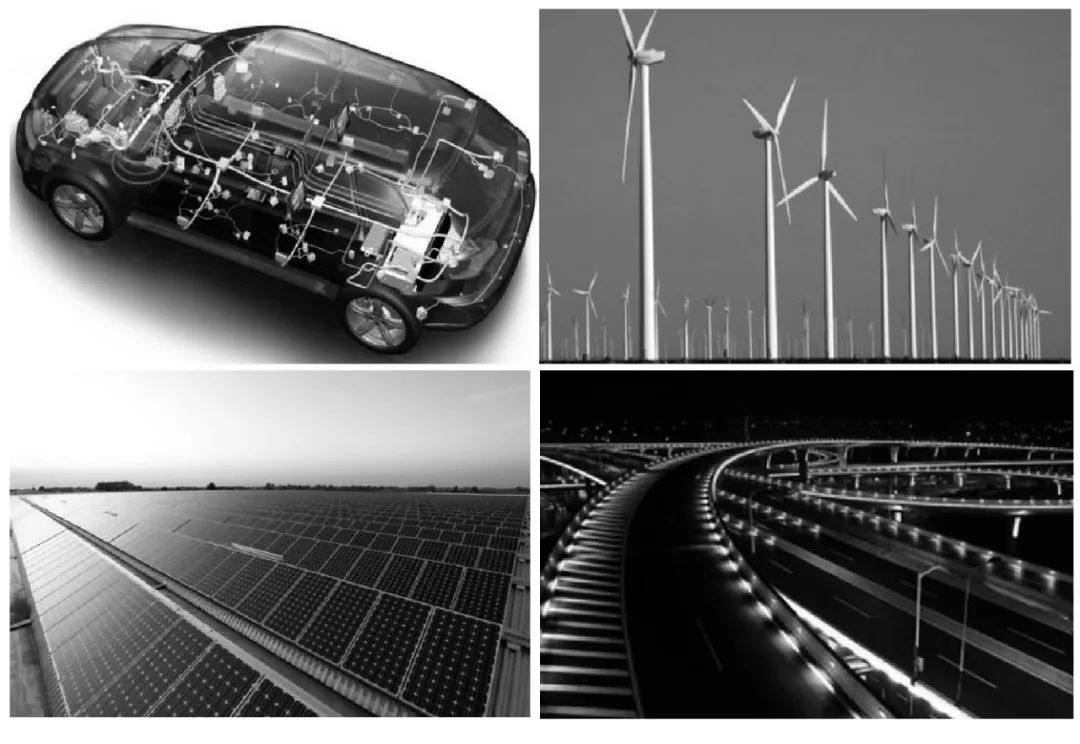
综上,陶瓷基板材料通常要求应具有以下性能特点:
-
优异的热导率。高的热导率代表了优异的散热性能,直接影响功率器件的运行状况和使用寿命;
-
高的力学性能。尤其材料抗弯强度和断裂韧性对功率器件可靠性有直接影响;
-
良好的绝缘性和抗电击穿能力。
-
低的热膨胀系数。与SiC衬底在热膨胀系数的匹配上具有其他陶瓷不可替代的优势;
-
良好的高频特性。即低的介电常数和低的介质损耗
-
表面光滑,厚度一致。便于在基板表面印刷电路,并确保印刷电路的厚度均匀
氧化铍(BeO)、氧化铝(Al2O3)、氮化铝(AlN)和氮化硅(Si3N4)四种材料是已经投入生产应用的主要陶瓷基板材料。
BeO陶瓷基板材料最突出性能是导热系数大,其室温热导率可达250W/(m·K),与金属铝相近,是氧化铝6~10倍。遗憾的是,由于BeO陶瓷的粉末有剧毒,伤口接触会难以愈合,长期吸入BeO粉尘会引起中毒甚至致命。此外BeO的毒性对周围环境也会造成污染,由此致使BeO陶瓷基板难以产业化。
作为技术成熟度最高的陶瓷基板材料,氧化铝基板综合性能较好,目前应用最成熟。Al2O3原料丰富、价格低廉,具有良好的绝缘性、化学稳定性及与金属附着性,是功率器件最为常用的陶瓷基板。但是因其热导率较低,仅为29W/(m·K),且热膨胀系数(7.2×10-6/℃)较高,强度低、介电常数高等不利因素限制其在大功率模块和集成电路中的应用。
AlN陶瓷基板具有高导热性、良好的绝缘性等特点,是目前Si基半导体材料中最为常用的陶瓷基板。但是AlN陶瓷机械强度低、易潮解以及较高的制造成本限制AlN基板的发展。
Si3N4陶瓷是综合性能最好的陶瓷基板材料,热导率可达90~120W/(m·k),热膨胀系数为3.2×10-6/℃,并具有优异的机械强度、良好的化学稳定性和抗热冲击性。尽管Si3N4陶瓷基板具有略低于AlN的导热性,但其抗弯强度、断裂韧性都可达到AlN的2倍以上,同时,Si3N4陶瓷基板的热膨胀系数与第3代半导体衬底SiC晶体接近,使其能够与SiC晶体材料匹配性更稳定。氮化硅是国内外公认兼具高导热、高可靠性等综合性能最好的陶瓷基板材料,这使Si3N4成为第3代SiC半导体功率器件高导热基板材料的首选。除BeO陶瓷基板外,其他3种陶瓷基板材料性能对比见表1。
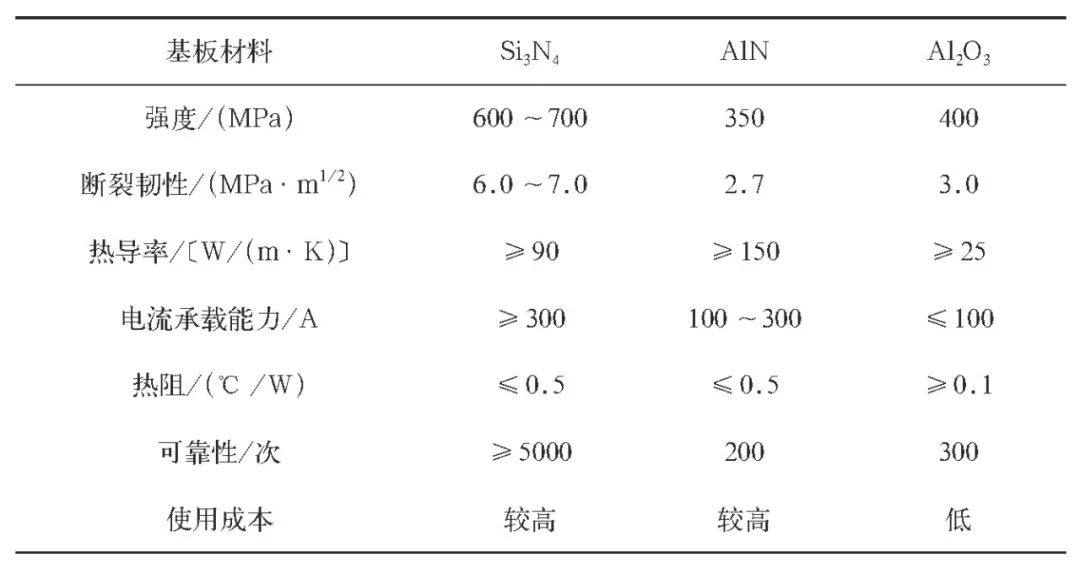
Si3N4陶瓷材料被认为是综合性能最好的结构材料。但是因其相对复杂的结构,可能形成较大的声子散射,导致Si3N4一度被定义为低热导率材料。值得庆幸的是,在1995年,Haggerty和Lightfoot等人借助固体传输理论,发现晶格缺陷和杂质是造成声子的散射,使得Si3N4的热导率低,并提出200~320W/(m·K)或许是β-Si3N4陶瓷热导率的极值,这也为氮化硅作为高导热材料提供了理论支撑。
无独有偶,借助分子动力学的方法,Hiroshi等重新计算了α-Si3N4和β-Si3N4单晶体的理论热导率,得出二者具有差异性的高热导率:α-Si3N4单晶理论热导率沿a轴为105W/(m·K),c轴为225W/(m·K);β-Si3N4单晶理论热导率沿a轴为170 W/(m·K),c轴为450W/(m·K)。1999年,Watar等人使用热等静压法制备了热导率155W/(m·K)Si3N4陶瓷材料,首次证明了Si3N4是一种极具潜力的高导热材料。但很遗憾,Si3N4陶瓷的实际热导率与理论热导率是有很大差距的,究其影响原因主要有:晶格排布和体相氧、物相组成、晶界相含量、陶瓷气孔及密度及其他杂质缺陷等。
原料粉体的粒度、纯度、物相是影响力高导热氮化硅陶瓷学性能、热导率的关键因素。内部杂质和晶格缺陷都会阻碍氮化硅陶瓷热导率的提升。要选择高纯度高的氮化硅原料,尤其避免引入氧(O)、铝(Al)元素。原因是,O元素可以形成晶格氧的晶格缺陷造成声子的剧烈散射,Al元素固溶于Si3N4,将Si替换,形成低热导率的Sialon相。不仅如此,原料粉体形貌也十分重要,小初始粒径、大比表面积、具备“自形”晶的粉体具有良好的烧结活性,易制备出高致密度的成品。
氮化硅的强共价键使得其很难通过固相扩散达到烧结致密的目的,需要加入一定的添加剂。但烧结助剂由于自身的性质,它的存在也会对氮化硅陶瓷材料的热导率造成不利影响,因此烧结助剂的选择应考虑3个方面:首先应考虑活性好的烧结助剂,含量尽可能的减少,降低形成的晶界相,不影响氮化硅陶瓷的致密度;其次应考虑在烧结助剂在烧结过程中形成液较低相粘度,有利于氮化硅的相变以及晶粒的长大;第3个方面应考虑烧结助剂形成的晶界相易于晶化,并形成高导热晶相。
烧结助剂主要分为氧化物和非氧化物2种,氧化物类烧结助剂最常见的为金属氧化物和稀土氧化物的组合。研究发现陶瓷材料晶界层厚度随稀土元素离子半径增大而增加,氮化硅陶瓷热导率随着烧结助剂稀土元素阳离子半径的增大而减小;含氧化钙(CaO)的烧结助剂与含氧化镁(MgO)相比,前者不利于氮化硅柱状晶的生长,硬度较高,材料热导率及强度普遍较低。
介于此,氧化物三氧化二钇(Y2O3)—MgO是制备是高导热氮化硅材料应用比较广泛的烧结助剂。在选择原料粉体时要尽量避免O元素的引入,烧结助剂的选择也遵从这一原则,可以减少晶界玻璃相、净化氮化硅晶格提高热导率及高温力学性能。因此,作为非氧化物烧结助剂的代表,氮化硅镁(MgSiN2)、氟化钇(YF3)等成为了制备高导热氮化硅陶瓷的常用助剂。研究表明:采用MgSiN2作为烧结助剂与采用MgO作为烧结助剂制备的氮化硅陶瓷相比热导率的提升约为15%。
为了制备具有各向异性的陶瓷材料,可以通过成型方法调控晶粒的排列和生长进行,保证晶粒在一维或二维方向上能够产生较好的定向效果。目前流延、轧膜、浇注和注射成型等高导热氮化硅基板的成型方法中,流延成型被公认为最适合于工程化制备技术。
Watari等人添加定量的β—Si3N4晶粒作为晶种,使用流延法制备出的氮化硅陶瓷中,Si3N4晶粒排列具有一定取向性。通过对烧结试样流延成型方向和垂直流延方向的热导率进行测试,发现热导率差距较大,分别为155W/(m·K)和52W/(m·K)。由此表明,氮化硅陶瓷具有各向异性,Si3N4晶粒排列也呈现取向性,不同方向热导率也不相同,并且在特定方向上具有较高的热导率。
近年来出现一种新型高效的织构化手段—将强磁场与基本成型方法复合的成型方法。依靠该方法,能够彻底实现陶瓷晶粒定向生长,且不受晶粒尺寸形貌和材料种类等元素的影响,研究表明磁场技术与陶瓷成型方法相结合是氮化硅基板成型技术重要的发展方向。
制备高导热Si3N4陶瓷材料的制备方法主要烧结方法主要有热等静压烧结(HIP)、热压烧结(HPS)、反应烧结重烧结(SRBSN)和气压压力烧结(GPS)。早期的研究多采用热等静压烧结方法,但是热等静压烧结存在设备昂贵、操作复杂、制备成本高等问题。
气压压力烧结、热压烧结和反应烧结重烧结烧结是目前制备高导热Si3N4陶瓷材料使用较多的烧结工艺。工程化制备主要采用气氛压力烧结和反应烧结重烧结烧结2种方法,分别针对以Si3N4粉体和硅粉为原料。Si3N4陶瓷的导热率的提高通常认为是与晶粒增大有关,因此通常选择高的烧结温度和长时间的保温环境促进晶粒生长。高温可以使α—Si3N4溶解沉淀向β—Si3N4发生相变,新生成的β—Si3N4晶粒晶格缺陷浓度较低,可以减少声子的散射,从而可以提升热导率。
现在国内还没有企业真正完成氮化硅基板产业化,各高校、研究院所和企业都在积极的进行产业化研究,目前实验室研制的Si3N4基板已达到或接近日本产品水平,国内多家企业正在加快产业化进程。同时,由于Si3N4基板还需要进行覆铜处理以及应用端考核,因此国内Si3N4基板要达到应用化水平还有一段距离。
中材高新材料股份有限公司(以下简称“中材高新”)的中材高新氮化物陶瓷有限公司(以下简称“中材高新氮化物公司”)在“十三五”国家重点研发计划支持下,系统研究并突破了高导热Si3N4基板制备的技术关键和工程化技术问题,通过Si3N4粉体改性处理、晶格氧含量及晶界相控制、微观组织定向排布等多种技术组合,以及突破了材料均化、成型、烧结、表面处理及覆铜除了等多个制备工艺技术,研制出及高导热、高可靠性于一体综合和性能优异的半导体绝缘基板材料,建立起年产10万片(114mm×114mm)中试生产线。Si3N4基板工艺流程见图2。
采用流延成型技术,通过Si3N4浆料性能指标优化,实现了Si3N4基板连续高效成型。流延板厚度可到达0.26~0.30mm,厚度可控制≤±5μm,见图3。
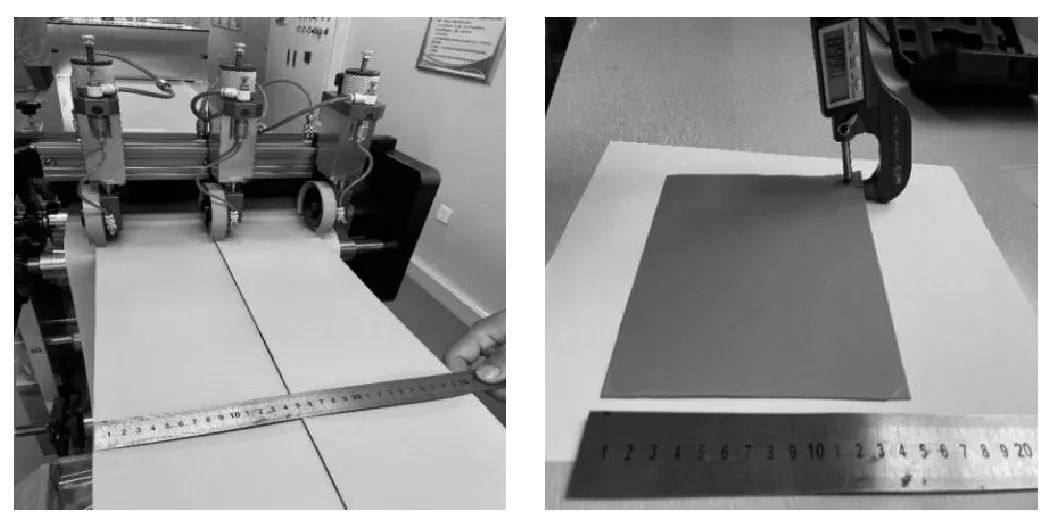
由于Si3N4烧结收缩较大(通常为18%~20%),且厚度尺寸很薄。因此控制其烧结变形是关键之一,通过对Si3N4基板变形主动控制,实现了气氛压力烧结致密化制备。Si3N4基板密度可达到3.20g/cm3(达到相对密度为99%)。烧结后的Si3N4基板见图4。
中材高新氮化物公司对Si3N4基板覆铜技术进行了系统研究,重点研究丝印及金属化工艺对覆铜板剥离强度的影响规律和热循环实验考核,见图5、6。热循环实验条件为:前1700次为-40~150℃,后300次为-50~170℃。
结果表明,中材高新氮化物公司制备的Si3N4覆铜板经过2000次循环后无可见开裂或剥离现象,具备优异的稳定和可靠性。
随着以SiC为衬底的第3代半导体芯片在新能源汽车、5G、新能源领域的快速推广,Si3N4陶瓷基板需求也迎来了快速发展阶段。国务院2020年发布的《新能源汽车产业发展规划(2021—2035年)》中也明确了新能源汽车在“十四五”以及未来的发展方向,强调要提升核心技术创新能力,完善质量保障体系和基础设施建设,健全产业生态,实施新能源汽车基础技术提升工程,突破效高密度驱动电机系统等关键技术和产品。全球及中国新能源汽车发展规划见图7。
根据图7所示,以2025年全球电动汽车年销售量为2500万辆计算,SiC功率器件的占比按照多家投资机构推测的数据占比37%为基准,按照现有电动车用Si3N4陶瓷基板为1标准片(7.5×5.5英寸)/辆,客车等大型车辆为2标准片/辆的用量计算,2025年高导热Si3N4基板的全球新增年需求量约为60万m2。
目前,全球范围内可实现批量化制造高导热Si3N4陶瓷基板的企业全部在日本。其中东芝材料(Toshiba Materials)产能达到10万m2/年、丸和(Maruwa)4万m2/年、电气化学(Denka)3万m2/年、京瓷(Kyocera)和日本精密陶瓷(JFC)1万m2/年。东芝材料的市场份额更是占到50%。中材高新氮化物公司制备的基板材料与日本各厂商产品指标对比见表2。
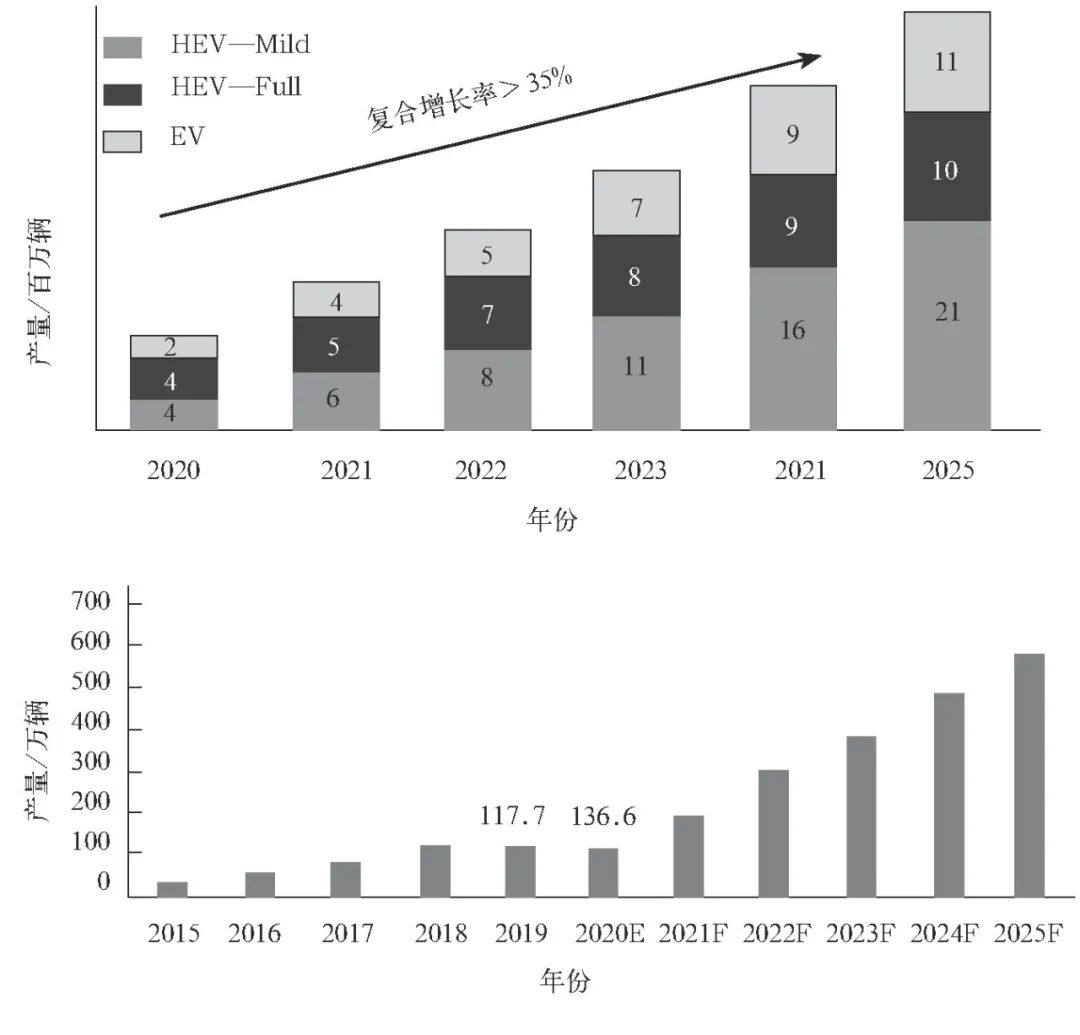
表2 高导热Si3N4陶瓷基板生产厂商产品指标对比

据相关报道,日本企业正在加快高导热Si3N4基板的产能,如日本东芝材料计划2022年之前将产能扩充至14.6万m2/年;日本电气化学投资1.62亿元用于高导热Si3N4陶瓷片的产能扩充,预计2025年全部建成;日本精细陶瓷株式会社计划在2023年之前将产能提高10万m2/a。2020年6月作为氮化铝基板全球领导者的日本德山公司,突然宣布进军Si3N4陶瓷材料,并公布他们已经开发了独有的节能、安全、环保且低成本的Si3N4基板生产技术。
日本日立、丸和、东芝的Si3N4基板和覆铜板产品图片见图8、9、10。
目前中材高新氮化物公司正在计划建设年产年产200t高端Si3N4制品项目,主导产品为热等静压Si3N4轴承球和高导热Si3N4基板,预计2022年投产。该项目的建成投产可填补我国在高导热Si3N4基板“卡脖子”的问题,实现自主可控,缩短国内外基板材料差距,有效提升国产大功率半导体器件的核心竞争力,服务支撑新能源汽车等战略性新兴产业的创新发展。
图11是中材高新热等静压Si3N4轴承球、图12是中材高新高导热Si3N4基板、图13是中材高新新建高端Si3N4生产厂房。
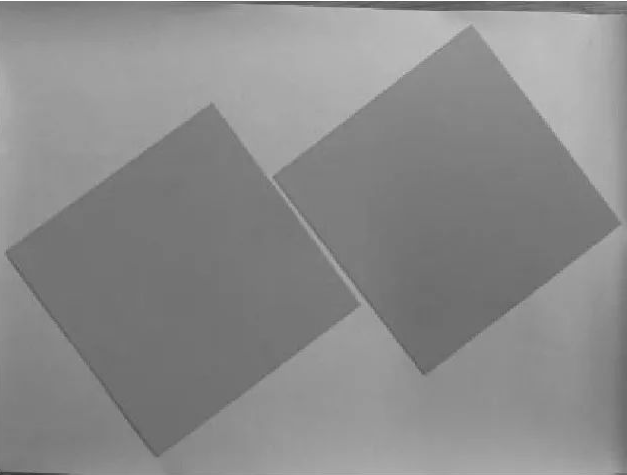
图8 日本日立Si3N4基板(规格114mm×114mm热导率125~130 W/(m·K))
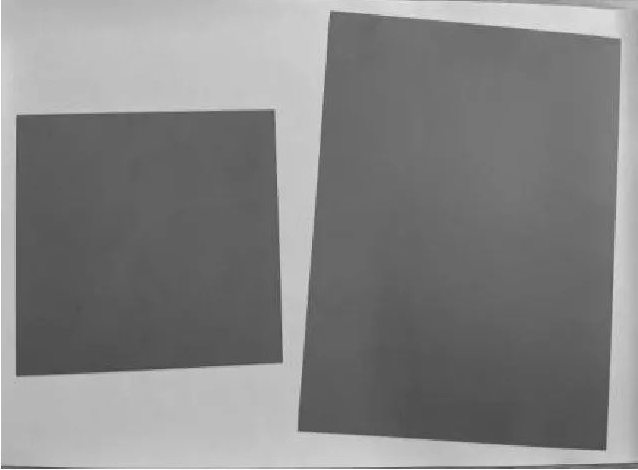
图9 日本丸和Si3N4基板(规格:114mm×114mm、190mm×138mm热导率80~85W/(m·K))
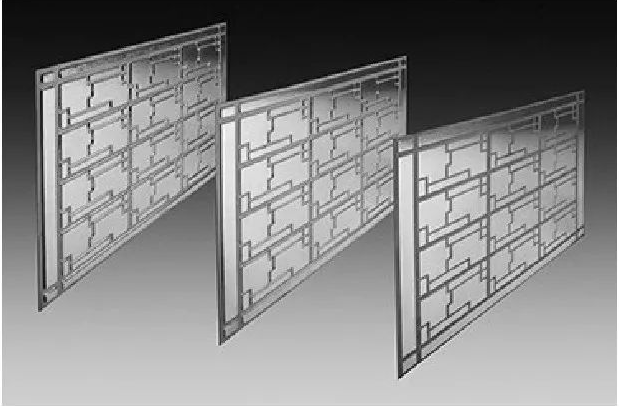
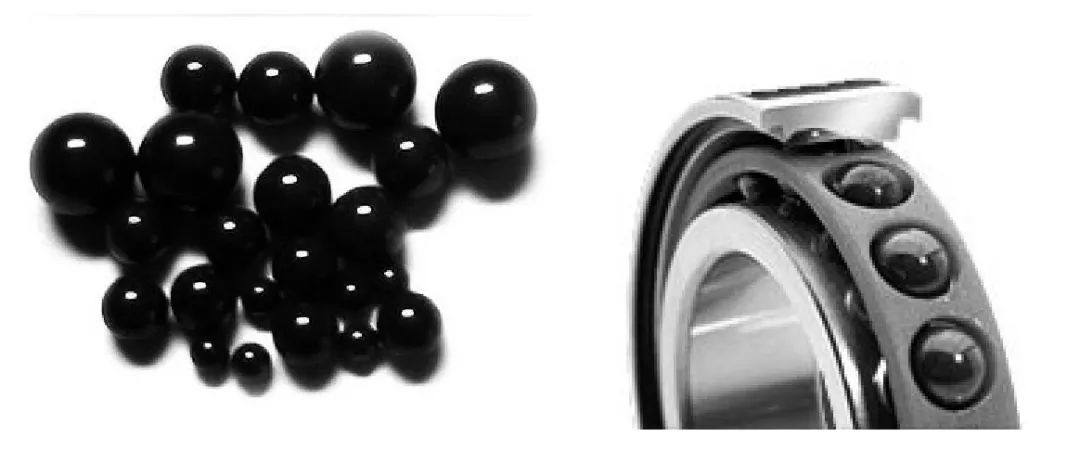
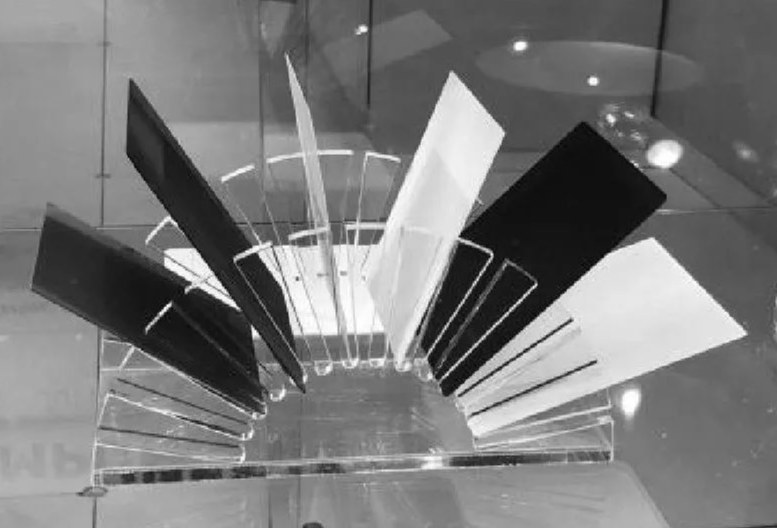
正是由于Si3N4陶瓷所具有的高热导率、高强度、高韧性以及较低的膨胀系数等综合性能,Si3N4被公认为第3代SiC半导体功率器件高导热基板材料的首选并取得了很好的应用效果。可以肯定。随着电动汽车、大功率电子电力器件的快速发展,Si3N4陶瓷基片必将迎来巨大的市场需求。我国在这一领域应进一步加强高校、科研院所和企业的协同合作,重点突破高导热Si3N4基板产业化关键技术和装备,全力打通Si3N4基板-精密加工-表面覆铜-考核应用产业链,尽快实现高导热Si3N4基板的国产化。
【解析】Si3N4的弯曲强度在600 MPa以上。
原文始发于微信公众号(陶瓷基板):中材高新 | 高导热氮化硅陶瓷基板最新进展