当前,随着微电子产业的飞速发展,对陶瓷材料有了更高的需求。HTCC材料制作的器件涵盖了广泛的应用领域。比如电子组件(多层电容器,多层执行器和R-C滤波器),3D多芯片模块(工程设计管理系统,汽车应用中的变速箱控制,航空航天和医疗工程领域中的高频应用),智能3D封装,微机电系统(MEMS)封装以及实验室芯片系统。
艾邦建有LTCC交流群,诚邀LTCC产业链上下游企业参与:
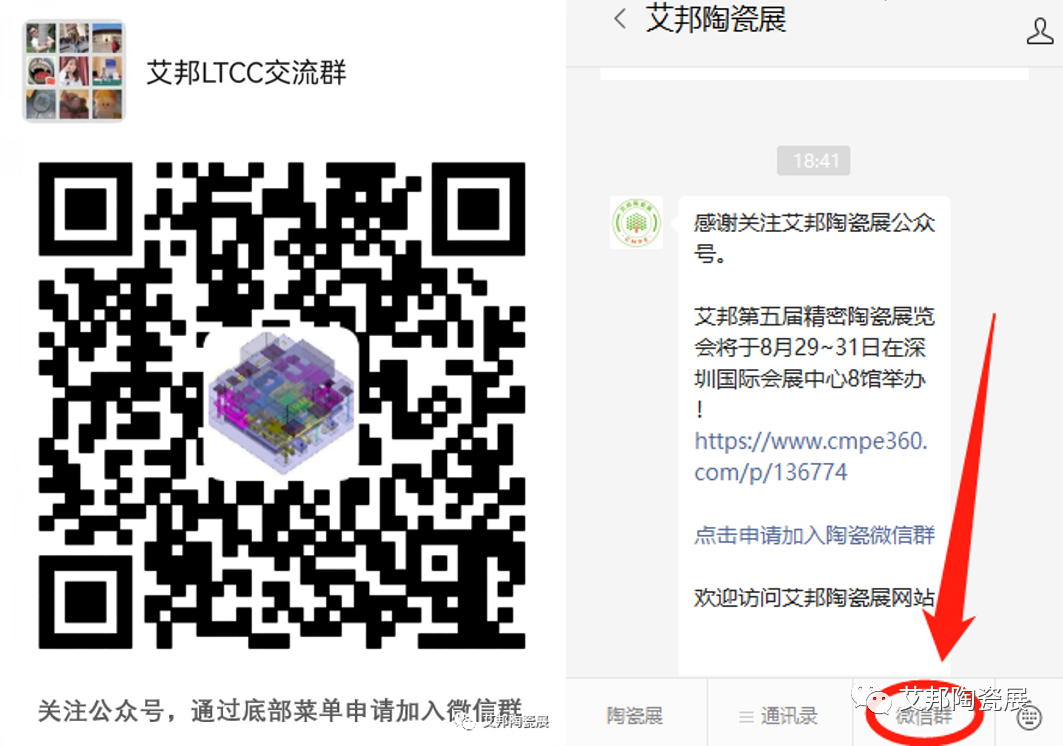
长按识别二维码关注公众号,点击下方菜单栏左侧“微信群”,申请加入LTCC交流群。
HTCC技术可实现密封的直通过孔密集的金属互连。因此HTCC技术常用于军事、航空航天、医疗器械、和高温领域,特别是在汽车、高功率、无线通信和RF封装方面。
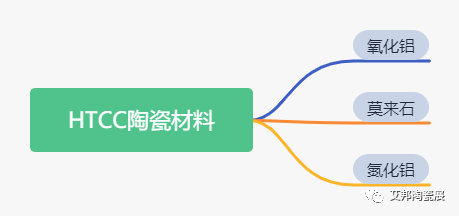
HTCC材料是在高于1500℃的环境下烧结而成。由于HTCC材料的热稳定性良好,所以它非常适合在超高温环境下的应用。
高温共烧陶瓷中较为重要的是以氧化铝、莫来石(主体为Al2O3-SiO2)和氮化铝为主要成分的陶瓷。常见的HTCC生瓷带有氧化铝陶瓷、氮化铝陶瓷以及氧化锆陶瓷等,采用流延法制备的生瓷带厚度一般为50μm到700μm不等。
在烧结过程中,陶瓷颗粒相变为致密材料,样品大约收缩15%到20%不等。其中,在超高温领域中,99.99%氧化铝高温共烧陶瓷的应用最为广泛HTCC氧化铝生瓷带的一些基本材料特性参数如下图所示。
生瓷坯在进行高温烧结的过程中往往会有一定的收缩比例,其收缩比例大约在15%-20%之间,为了使本论文设计的传感器达到设计要求以及性能要求,在烧结前,必须给生瓷坯按照收缩比来计算尺寸,防止其最终产品达不到要求。
氧化铝陶瓷技术是一种比较成熟的微电子封装技术,它由92~96%氧化铝,外加4~8%的烧结助剂在1500-1700℃下烧结而成,其导线材料为钨、钼、钼一锰等难熔金属。
该基板技术成熟,介质材料成本低,热导率和抗弯强度较高。但是,氧化铝多层陶瓷基板有下列缺点:
(3)热膨胀系数与硅相差较大,从而限制了它在巨型计算机上的应用。
莫来石的介电常数为7.3-7.5,而氧化铝(96%)的介电常数为9.4,高于莫来石,所以莫来石的信号传输延迟时间可比氧化铝小17%左右,并且,莫来石的热膨胀系数与硅很接近,所以这种基板材料得到了快速发展。
例如日立、Shinko等公司均开发了莫来石多层陶瓷基板,并且其产品具有良好的性能指标。不过此基板的布线导体只能采用钨、镍、钼等,电阻率较大而且热导率低于氧化铝基板。
对于氮化铝基板来说,由于氮化铝热导率高,热膨胀系数与Si、SiC和GaAs等半导体材料相匹配,其介电常数和介质损耗均优于氧化铝,并且AlN是较硬的陶瓷,在严酷的环境条件下仍能很好地工作。
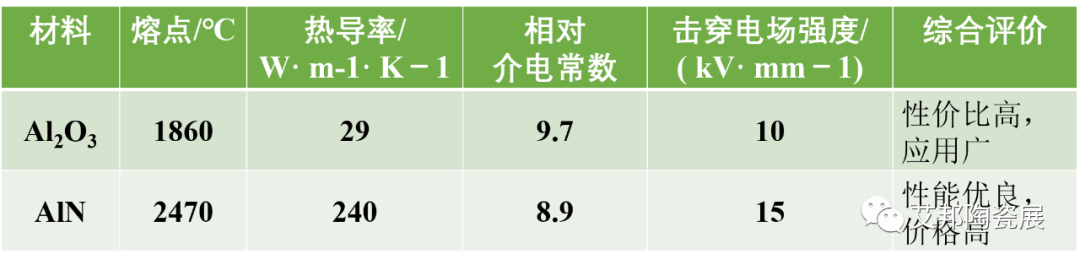
(3)氮化铝基板与钨、钼等导体共烧后,其热导率有所下降;
(4)丝网印刷的电阻器及其他无源元件不能并入高温共烧工艺,因为这些无源元件的浆料中的金属氧化物,会在该工艺的还原气氛下反应而使性能变坏;
(5)外层导体必须镀镍镀金保护其不被氧化,同时增加表面的电导率并提供能够进行线焊和锡焊元器件贴装的金属化层。
虽然有这些缺点,但从总体上来说,氮化铝基板比其他高温共烧陶瓷基板有更多的优势,在高温共烧陶瓷领域有很好的发展前途。主要应用在传感器封装、表面贴装封装、MEMS封装、光通信封装、LED封装等。
HTCC不同的材料组成决定了其不同的应用,相应的其材料的缺点也在某种程度上限制了应用。HTCC陶瓷粉体材料厂家主要有:东曹、住友、艾森达、扬州中天利等企业。
整体而言,HTCC基板具有结构强度高、热导率高、化学稳定性好和布线密度高等优点,因此在当前大功率微组装电路中具有广泛的应用前景。
6月30日,佳利电子研究院院长/常务副总胡元云将带来做《HTCC技术发展及封装陶瓷应用》主题报告分享,欢迎各位行业朋友与会交流
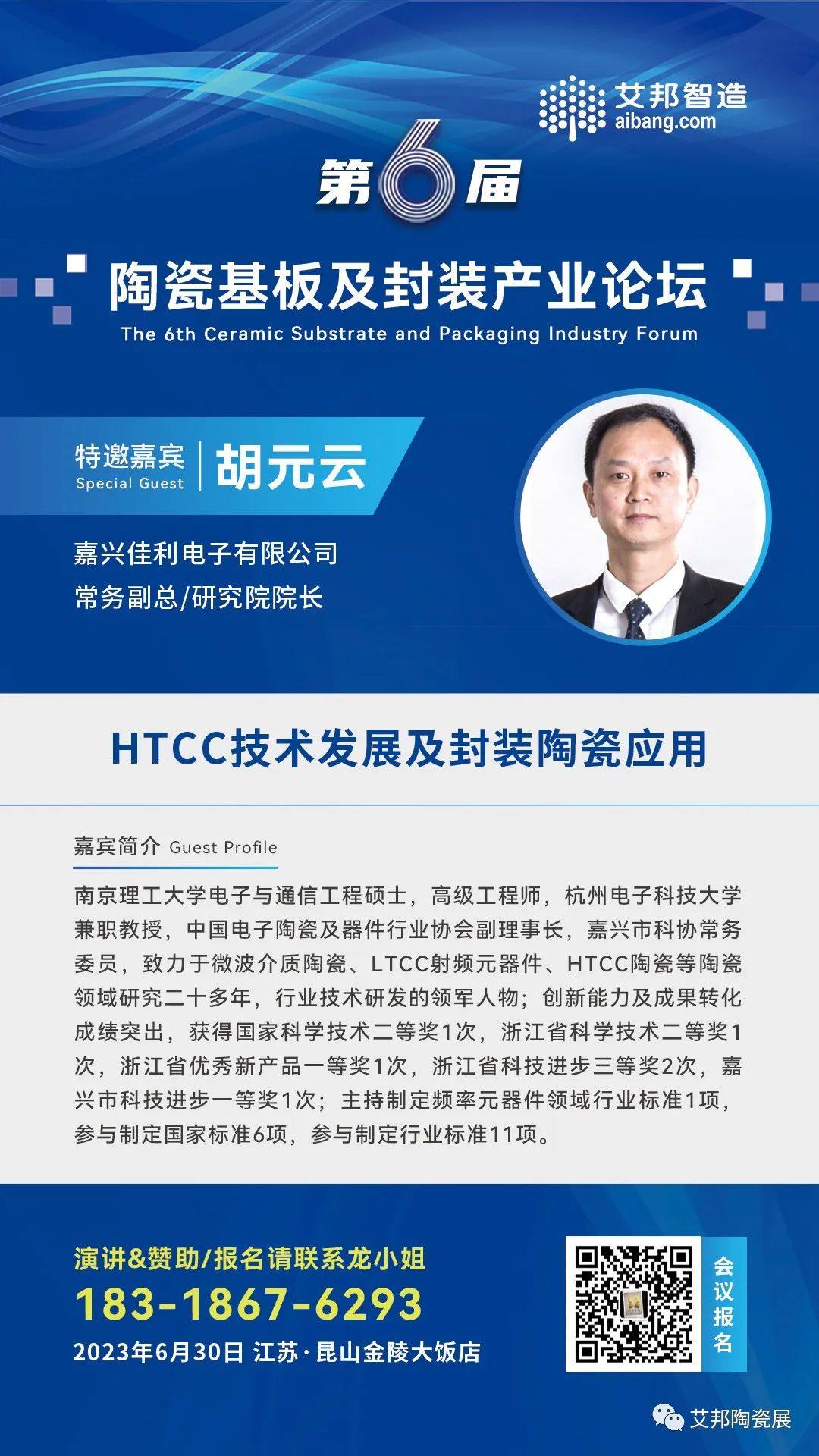
原文始发于微信公众号(艾邦陶瓷展):HTCC高温共烧陶瓷材料介绍