1.碳化硅模块的封装
封装本质上是芯片布局成电路和散热技术。结合外部设计组成成熟的产品,其技术基础主要是三个方面。包括芯片互连,芯片焊接,和散热设计,加上一个外壳封装构成整个模块。
无论框架型模块基本结构,还是塑封型模块结构,主要为半导体芯片提供四个方面的功能:电气连接、机械支撑、散热途径和环境防护。在提供这四个功能同时也引入了一系列的问题,包括寄生参数(指寄生杂感、寄生电容的问题),连接问题(主要指芯片到DBC、DBC到外面的端子连接等信号端的震动问题、发热问题以及接触性问题),热阻和界面失效。
图片来源 :SiC 功率模块封装技术及展望 蔡蔚 ,杨茂通 ,刘 洋 ,李道会
①基础材料
● 塑封材料(环氧树脂、硅胶):环氧树脂、硅胶,还有整个模块的外框结构以及散热器材料。
②封装工艺
● 端子叠层连接工艺(激光焊接):比如铜带焊接、铝带焊接、端子与外围连接的激光焊接
③模块设计
通过有效的热、电、力、磁的联合仿真来设计高效率、高压、高温、高功率密度的模块,最后进行可靠性测试及失效分析。
2.模块的封装需要解决的问题
①电学性能,包括杂感、电流均流、EMI、信号串扰,以及绝缘和爬电的问题;
②热管理性能,主要研究稳态和瞬态的热阻、比热容、热耦合的问题,以及整个冷却系统的流体压降,热管理性能直接影响了整个模块的可靠性。
③机械性能,主要是机械的抗震性以及系统高集成的设计。机械振动方面,采用超声波端子焊和激光焊之后解决了汽车模块对机械强度的要求,随机振动10g,冲击振动50g。
④可靠性,主要包括功率循环、温度循环、高温存储以及高温高湿的反偏问题等。
芯片技术趋势:
更高工作结温
封装技术趋势:
更优背面散热:更优散热流道设计,结合低热阻封装方案,提升器件出流能力
框架封装--耐受更高温度,更高功率密度,更小模块体积,更低电感设计
转模封装--适用高结温应用 (SiC芯片),高良率,低成本,满足客户定制化应用场景 (单管、半桥),调研发现,目前30千瓦以下的功率模块封装主要使用碳化硅器件,180千瓦以下主要采用标准框架式灌封封装技术,而180千瓦以上逐渐开始采用塑封工艺技术。
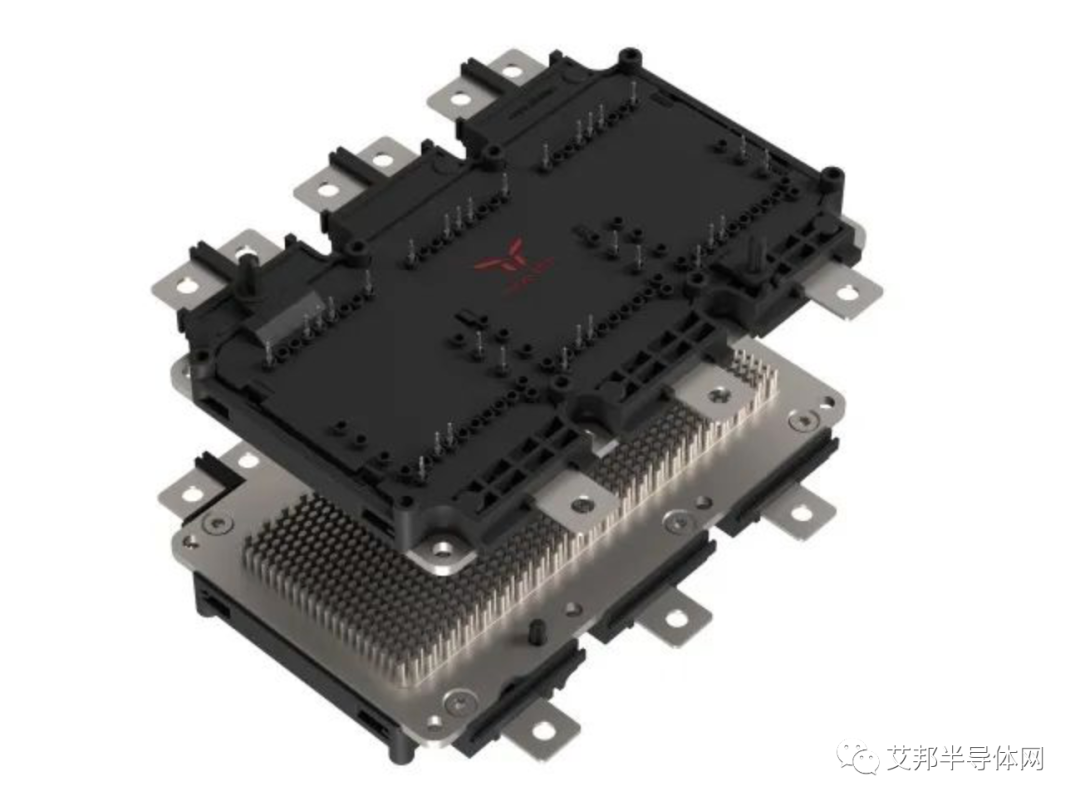
框架灌封式碳化硅功率模块
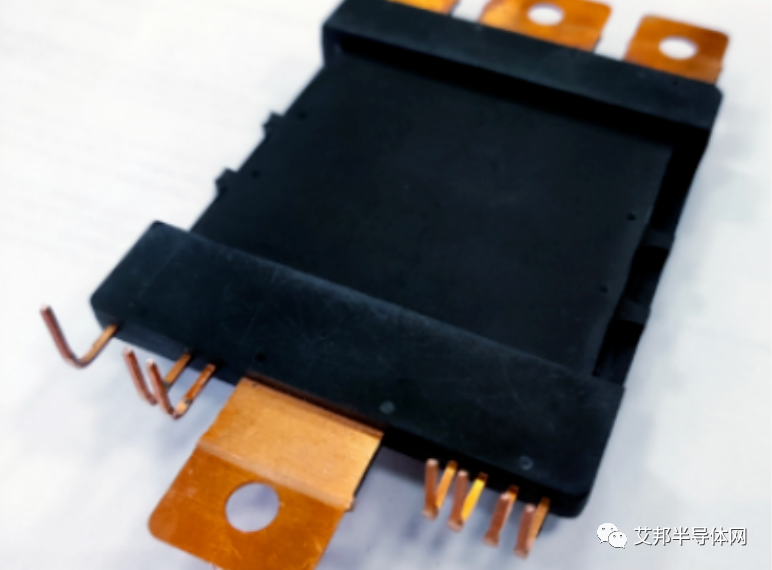
塑封2in1功率模块A样件,红旗
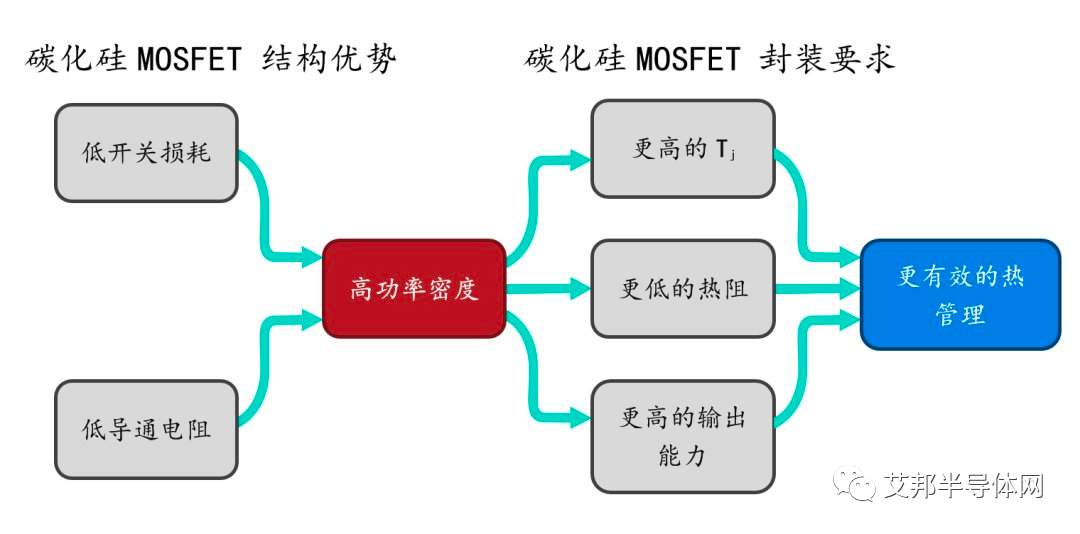
Tesla Model 3功率模块
资料来源:http://www.hs-mmcs.com/contents/8/427.html
3.碳化硅模块的生产工艺流程
碳化硅功率模块的生产工艺流程主要包括陶瓷基板排片、银浆印刷、芯片贴片、银烧结、真空回流焊、引线框架组装焊接、引线键合、等离子清洗、塑封、X光检测、测试包装等环节。
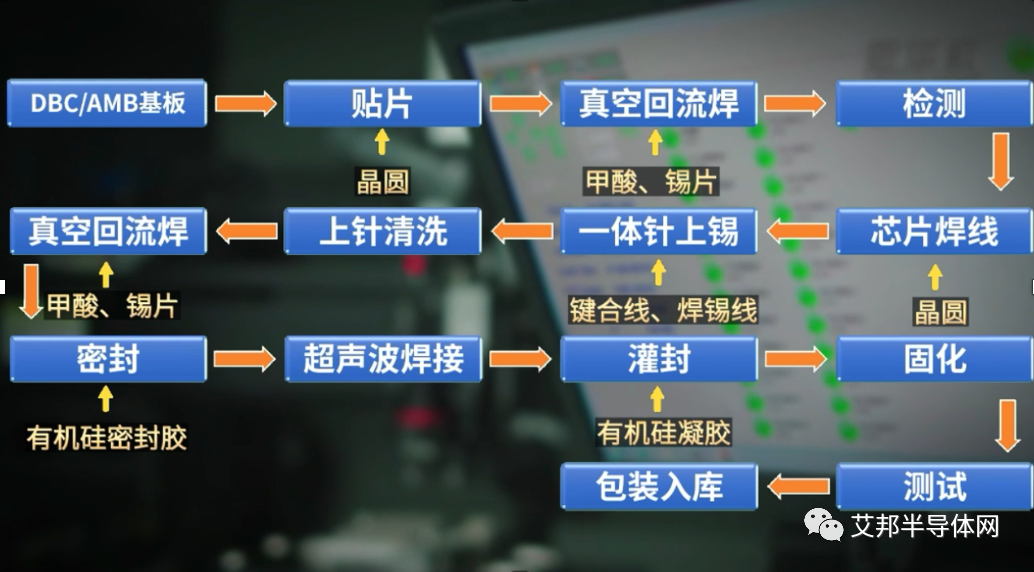
碳化硅半桥模块的生产工艺流程图
资料参考:苏州斯科半导体环评报告
4.碳化硅模块与IGBT封装区别
在 IGBT 时代,封装技术基本可以用“焊接”和“邦定”加以概括。
首先,功率芯片的表面金属化多为铝质(Al)或铝掺杂硅(AlSi);
焊接的材料多为“锡银铜”(SnAgCu,SAC 焊料),工艺多为各类钎焊(Brazing);
邦定,功率引线多用粗壮铝线或铜带(或编织铜网)等 ;
上图显示了一个沿用传统的 IGBT 封装工艺的 SiC 模块(单相)。该封装工艺的 die Attach 及 DCB Attach,使用了钎焊技术,熔点仅为 220°C 上下。SiC 芯片使用铝质表面金属化,因而铝基同质邦定(Al-Al)的寿命尚可,但 die Attach 和芯片顶部到 DCB 的邦定是铜铝结合(Cu-Al),剪切力在 20~30MPa左右,其宽幅度热冲击(TST)和热电联合功率循环(Power Cycling)的周次能力不足,因而在碳化硅的高耐受结温应用的情况下,寿命不足。
参考资料来源:https://data.angel.digital/pdf/cs_china_2022_feb_march.pdf
在发展的早期阶段,碳化硅功率模块自然而然地继承和沿用了 IGBT 的封装技术,但由于碳化硅器件的不同特性,且随着应用需求的相应提升,旧有的封装技术越来越难以满足要求,主要表现在 :
1)更高熔点 :过去各类焊接的熔点大约都在 220°C 左右 ;现在碳化硅器件的最高耐受结温普遍都在 175°C,不久将会普及到 200°C,因而,要求各类连接的熔点必需超过 300°C,最好达到400°C 以上 ;
2)更佳热导 :虽然碳化硅芯片内阻和开关损耗都显著的降低了,耐受结温也高于 IGBT,但是开关频率的提高和芯片面积的减小,还是导致发热密度急剧增加。这样,在同等功率条件下,要求单位面积的导热能力提高 3~7 倍 ;因而,碳化硅模块需要更佳的导热结构设计并采用先进的材料,使得模块总体热阻最小,热导率最大 ;
3)连接更坚固 :碳化硅功率模块需在更大温度范围内工作,因而需要把各个连接的剪切力提高到 60MPa 或以上 ;具体实现,同样涉及到新型材料和工艺过程设计和实施 ;
4)降低连接电阻 :连接的电阻要降低,以便在有限的面积(IGBT 的 1/5)上承载相当的电流,降低耗散 ;
IGBT常见封装工艺流程
现 SiC 封装技术大多沿用硅基器件封装方式,基于传统封装结构,碳化硅模块 封装主要会带来以下两方面问题:
1)引线键合,复杂内部互联结构会产生较大的寄生电容/电感。SiC 器件由于具有高频特性、栅极电荷低、开关速度块等因素,在开关过程中电压/电流随时间的变化率会变得很大(dv/dt;di/dt)。因此极易产生电压过冲和振荡现象,造成器件电压应力以及电磁干扰问题。
2)高工作电压以及电流下的器件散热问题。SiC 器件可以在更高的温度下工作,但在相同功率等级下,SiC 功率模块较 Si 在体积上大幅降低,因此 SiC 器件对散热的要求更高。如果工作温度过高会引起器件性能下降,不同封装材料热膨胀系数失配,进而出现可靠性问题。这意味功率模块需要更多地依赖封装工艺和散热材料来进行散热。
SIC芯片封装技术重要发展方向有几个点,包括改善产品的功率循环能力,提高寿命;降低模块杂散参数,优化产品电气特性;改善散热性能,提高工作结温,增加功率密度。
5.碳化硅模块的封装设计方向
目前新的设计SiC模块的设计方向是结构紧凑更紧凑,通过采用双面银烧结和铜线键合技术,以及氮化硅高性能AMB陶瓷板、用于液冷型铜基PinFin板、多信号监控的感应端子(焊接、压接兼容)设计,努力往低损耗、高阻断电压、低导通电阻、高电流密度、高可靠性等方向努力。通过好的设计和先进的工艺技术确保碳化硅MOSFET性能优势在设备中得到最大程度发挥。
1)双面散热技术
双面散热的功率模块封装结构可以通过取消金属键合线,增加缓冲层并对缓冲层的形状、材料、尺寸的优化,可减小杂散电感,增加散热途径,降低功率模块中芯片所承受的长时间高温危害,提高模块的使用寿命。
2) AMB基板
基板主要趋势是使用高性能材料,减少层数和界面的数量,同时保持电、热和机械特性。绝缘金属基板(IMS)和 IMB 基板仅用于中低功率模块,如 EV/HEV 等。主流材料正逐渐从直接覆铜(DBC)转向活性金属钎焊(AMB)活性焊铜工艺,AMB是DBC工艺技术的进一步发展,工作原理为:在钎焊电子浆料中加入少量的活性元素(Ti,Zr,V,Cr等),采用丝印技术印刷到陶瓷基板上,其上覆盖无氧铜后放到真空钎焊炉内进行烧结,然后刻蚀出图形制作电路,最后再对表面图形进行化学镀。
功率模块中主要使用3种陶瓷覆铜板:AL2O3-DBC热阻最高,但是制造成本最低;AlN-DBC热阻最低,但韧性不好;Si3N4-AMB陶瓷材料热阻居中,韧性极好,热容参数也更出色,可靠性远超AlN和AI2O3,使得模块散热能力、电流能力、功率密度均能大幅提升,其与第三代半导体衬底SiC晶体材料的热膨胀系数更为接近,匹配更稳定非常适合汽车级的碳化硅模块应用。AMB陶瓷基板有望成为IGBT和SiC器件领域新趋势。
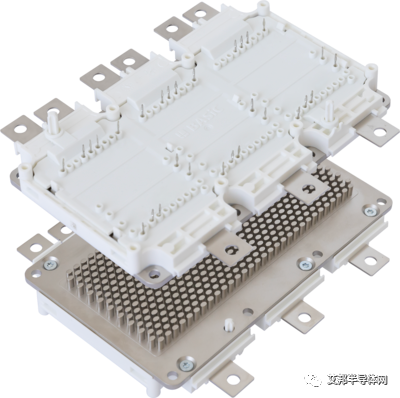
采用氮化硅AMB绝缘基板的模块(来源:基本半导体)
图片来源:https://www.basicsemi.com/h-pd-26.html
3) 银烧结
银烧结封装技术会是功率模块互连的主流技术。由于银离子迁移对互联结构有负面影响,加之成本和热应力适配需求,与银烧结技术类似的瞬时液相烧结(TLPS)银铜烧结铜烧结技术和相应的焊浆材料也在快速发展,部分技术瓶颈有望在近几年突破。
银烧结或铜烧结熔点高,界面连接强度高,导电导热好,保证在“热-机械”循环应力下的高可靠性
银烧结是目前碳化硅模块领域最先进的焊接技术,可充分满足汽车级功率模块对高、低温使用场景的严苛要求。
传统引线键合及焊料问题
- 引线缠绕
- 循环易疲劳,可靠性低
- 熔点<300℃,不适合高温器件互连
- 金锡材料高温脆性产物,降低可靠性
银,铜烧结技术优势
- 低温烧结(<300 ℃高温服役)
- 厚度较传统焊接层厚度薄6 0%~7 0%,适合高温器件互连电性能(4.1X107 S/m、热性能(240 W/mK)均优于无铅焊料.电导率提高了 5~6倍,热导率提高了3~4 倍
- 模块可靠性表现更好,寿命更长
很多企业已经尝试将功率模块内部中的所有传统焊料升级迭代为银烧结工艺,包括芯片,电阻,传感器等。
DTS (Die Top System) 技术原理
为进一步提升模块电性能及可靠性,尝试的方向是采用DTS+TCB(Die Top System + Thick Cu Bonding)技术,在常温条件下通过超声焊接将粗铜线与AMB基板、及芯片表面的覆铜片进行键合连接,实现彼此间的电气互联。相较铝线键合,模块寿命可提升3倍以上,且电流和导热能力可大幅提升。
https://www.heraeus.com/en/het/products_and_solutions_het/material_systems/die_top_system/dts_page.html
4) Cu Clip
在进行芯片正面连接时可用铜线替代铝线,消除了键合线与 DBC 铜层之间的热膨胀系数差异,极大地提高模块工作的可靠性。铝带、铜带连接工艺因其更大的截流能力、更好的功率循环以及散热能力,也有望为碳化硅提供更佳的解决方案。
Cu Clip即铜条带,铜片。
Clip Bond即条带键合,是采用一个焊接到焊料的固体铜桥实现芯片和引脚连接的封装工艺。
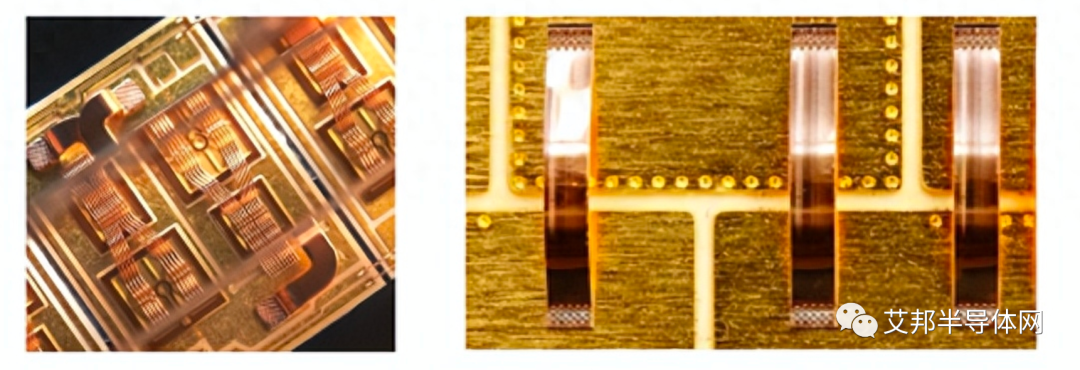
铜键合线(左)、铜带连接(右)
资料来源:http://www.hymexa.com/html/fzjsys/19.html
与传统的键合封装方式相比,Cu Clip技术优点:
1、芯片与管脚的连接采用铜片,一定程度上取代芯片和引脚间的标准引线键合方式,因而可以获得独特的封装电阻值、更高的电流量、更好的导热性能。
2、引线脚焊接处无需镀银,可以充分节省镀银及镀银不良产生的成本费用。
3、产品外形与正常产品完全保持一致。
5) 热管理
更集成的封装结构设计以及电路拓扑,以进行更好的系统热管理
为使模块产品热路径设计更紧凑,促使逆变器系统集成设计更紧凑高效,进一步降低整体系统逆变器成本,通过封装形式的改变,改善散热性以及通流能力。
采用多芯片并联的内部结构,各并联主回路和驱动回路参数基本一致,最大程度保证并联芯片的均流性。
模块内部封装有温度传感器(PTC),且PTC安装在靠近芯片的模块中心位置,得到了一个紧密的热耦合,可方便精确地对模块温度进行测量。
6) 外壳材质
IGBT模块的塑封材料基本上采用PBT或PPS,但也有采用PPA、PA、LCP等材料的情况。在耐温要求不高的情况下,PBT仍然是被广泛采用的材料。然而,对于高耐温要求的器件,例如SiC运行功率较高的情况下,通常需要采用高温材料PPS或9T。
原文始发于微信公众号(艾邦半导体网):碳化硅模块封装技术概述
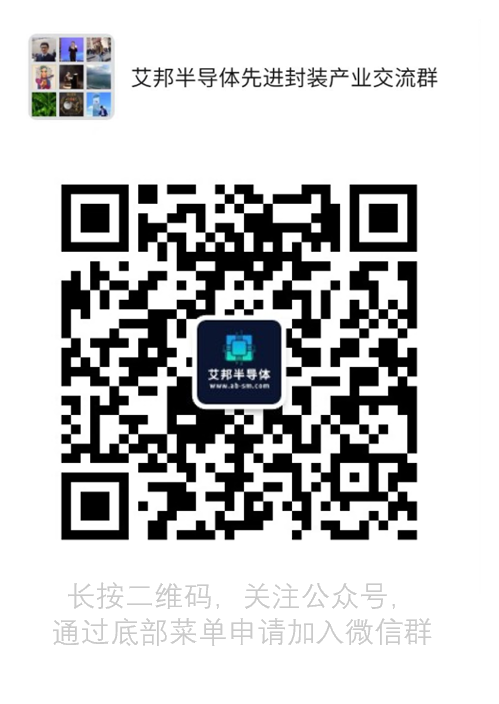